Putting greens with poor drainage are prone to problems when heavy rain and hot weather combine. Poorly drained greens tend to have poor soil oxygen, which is crucial for root health. As Al Schwemler, property manager, Toronto Golf Club, likes to say: “Drainage is one of the fundamentals for good greens.”
Toronto Golf Club, designed by Harry S. Colt, is North America’s third oldest club (1876). It recently underwent a complete renovation. As part of the long-range plan, the club added new subsurface green drainage to all 18 holes, plus the practice green. Like many of the tracks built in the late 1800s and early 20th century, it features old pushup greens, which were built with little consideration for drainage.
“We had good surface drainage on these old Colt greens, but there was no subsurface drainage,” Schwemler says. “When doing our long-range plan, green drainage wasn’t initially part of the project, but I threw this in from an agronomic standpoint. It was going to be a $200,000-plus job though, so the club put it on hold. Then, when the whole project came in under budget, they put it back in.”
In 2009, Toronto Golf Club literally rebuilt its course – from new tee decks and bunkers to new grass in the rough, green expansions and a brand new irrigation system to name a few of the many changes the historic property made. It was the perfect time to install new green drainage as the course was closed from July 2009 to May 2010. The club hired TDI Golf and its XGD (Existing Greens Drainage) division, to install a subsurface drainage system to remove surface water more rapidly and lower the water table, thereby improving turf growth. The procedure has gained a lot of recognition and popularity in the turf industry as an excellent method of improving the subsurface drainage of existing greens without rebuilding them.
“Conventional golf drainage theories rely on surface water as the primary focus, but this is absolutely false,” explains Mark Luckhardt, vice-president, XGD, who helped develop and perfect TDI’s XGD process more than 18 years ago. “We need to look at groundwater table issues first and foremost. XGD drainage is based on similar farm drainage practices which relies 99 per cent of the time on groundwater table lowering, and very few open surface inlets or catch basins. Every single mile of this simple, yet effective, drainage installation relies on controlling the subsurface groundwater table down to a manageable level out of the crop root zone.”
This was the first time XGD had done an entire course. Schwemler says what was most interesting for them, because Toronto Golf Club has a sandy soil profile on the property, is that XGD backfilled the club’s green drainage with their native soil. “If you put a blend of sand/peat back in the trenches, when you get hot, dry conditions, you can start to see those trenches,” Schwemler says.
After only one season, Schwemler says he doesn’t have any scientific proof as to the effectiveness of the new drainage, but he does have a superintendent’s feel. “They are working great,” he says. “Our soils drain significantly quicker and our greens are firming up faster after a series of rain events. It’s also bringing more oxygen down to the soils, which should help reduce diseases and make the turf healthier in the long run.”
The greens drainage project cost about $230,000 for all 19 greens. The work was spread out among the entire renovation project with each green taking approximately five days to complete.
“The XGD system is a permanent solution to poorly drained and compacted greens, leading to increased aeration and the removal of excess moisture,” Schwemler says. “The result is a revived green without the need for expensive and disruptive reconstruction. No other system minimizes the disruption to the green as XGD does, which ensures the surface is back in play as soon as possible. It was a great investment for our club.”
DOING MORE, WITH LESS. Like most superintendents, Garrett Luck’s budget is tight these days The greenkeeper at North Shore Country Club in Mequon, Wis., recently developed a master plan to renovate the entire course. Part of his long-range plan included a complete rebuild of North Shore’s greens.
But during the course of interviewing architects, the club decided they weren’t willing to spend the money needed to rebuild the greens. “Our members were happy with the conditions and subtleties of these old push-up greens,” he explains. “But, we had about four inches of top dressing on top of a mucky soil, so our greens drained poorly … we still needed to address this issue.”
Since a complete greens rebuild to USGA specs was out of the question due to the cost, Luck looked for alternatives. That’s when he discovered Golf Preservations, who the club hired to install green drainage on all 27 of its holes.
“At the onset, I thought it would be an improvement, but not nearly to the level that a complete rebuild would be,” Luck says. “It has been a dramatic improvement, surpassing our expectations in the ability of the greens to drain. For example, after a hard rain, we used to have standing water on 30 per cent of the greens. Since Golf Preservations installed the new drainage, now, within 20 minutes, the green surfaces are completely clear.”
Luck used the opportunity of the greens being out of play to reseed them with a high-quality bentgrass; their consulting architect also added some subtle contours to give the greens a little more interest on a select number of holes. “The members are very pleased,” says Luck. “The balls don’t plug now and they roll more smoothly. And, we can now mow and roll more quickly following rain events.”
Samson Bailey, Golf Preservations’ president, says the key to any green drainage project is choosing the right sand mix. “I recommend guys keep a sand mix that matches as closely as possible to their top three to four inches of aerifying mix. Most of the time, I tell clients to stay between two to four inches an hour on their sand mix. A lot of guys in the earlier days went sandy and now they have problems with their drainage lines showing up.”
The first thing Bailey’s crews perform is a survey to understand each green’s topography. “Each green is unique,” he explains. “We design a drainage pattern by using the natural contour of the green; then, we try to catch as much surface and ground water as we can. After we’ve used lasers to get the topography, we design a specific drainage layout for each green.”
After the topography is determined, Bailey says the next step is to install six-foot centers to provide consistent drainage throughout the green.
This is followed by hand removing the sod in seven inch by 15 inch strips and placing plywood before trenching, Bailey says. The grade is then checked before installing two-inch perforated pipe with micro-slits to a depth of between 15 and 16 inches. The pipe is covered with a 6-2-2 greens mix to help direct the water into the system, he adds.
“After the mix is hand tamped in place, the sod is returned to its exact location to prevent shrinkage,” says Bailey. “The sod is tamped level, the green is cleaned with blowers, and the green is immediately ready to roll, mow and play.”
So, don’t let Mother Nature wreak more havoc on your course than is necessary following a heavy storm. Take preventative measures now to tackle any subsurface greens issues your facility may have and make sure surface water drains away, rather than remains on the green.
Your members will thank you. GCI
David McPherson is a freelance writer based in Toronto.
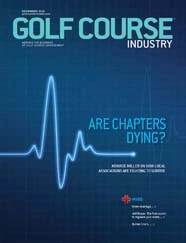
Explore the December 2010 Issue
Check out more from this issue and find your next story to read.
Latest from Golf Course Industry
- Golf Construction Conversations: Reed Anderson
- ’Twas the Night Before Christmas (on turf)
- Twas the Night Before Christmas (the turf version audio)
- Advanced Turf Solutions and The Aquatrols Company release soil surfactant
- Heritage Golf Group acquires North Carolina courses
- Editor’s notebook: Green Start Academy 2024
- USGA focuses on inclusion, sustainability in 2024
- Greens with Envy 65: Carolina on our mind