An old golfing adage holds that if you don’t like the condition of the bunkers, don’t hit your ball into them. The real problem with bunkers is that they are, like the rest of the golf course, ever-changing entities. Even with the best drainage systems, bunkers can succumb to soil contamination and washed out sand during hard rains.
Bunker liners are growing in popularity as a potential remedy for some of the worst problems bunkers suffer. Here are some pointers and tips on how to use them most effectively.
Do Your Homework. Mike Hurdzan, principal at Hurdzan/Fry Design in Columbus, Ohio, says it’s critical for superintendents to do their homework before deciding which bunker liner is best for their conditions. He recommends digging test bunkers and applying the different products and sands to ensure the proper product is used.
“You have to do a proper cost-benefit analysis of bunker liners because if you don’t, you’ll be sorry,” Hurdzan says. “So many factors come into play when evaluating these products. It pays in the long run to do a thorough investigation.”
There are a number of factors to consider, including weather conditions – freezing and thawing can affect the way bunker liners perform – irrigation water quality, number of bunkers, maintenance labor, installation cost and sand quality and shape.
Bunker liners are most effective when they are added as a drainage aid. Hurdzan says. “What you’re hoping to do is channel the water during hard rains into the drainage system to keep puddles from forming in the bottom of your bunkers,” he says.
Chuck Hutton, sales representative for SandTrapper, says sand inconsistency is one of the most common complaints about bunkers. Bunker liners, because of their drainage capabilities, offer superintendents a chance to take that off golfers’ lists, he says.
“When the bunker drains more quickly, the sand is more consistent,” Hutton says. “You can offer golfers the same shot values from a bunker because the sand will have the same moisture content throughout.”
Geotextiles. There are primarily two different types of liners on the market today – geotextile fabrics (such as those produced by SandMat and SandTrapper) and polyurethane sprays that bind the soil substrate together (manufactured by companies like Klingstone).
Geotextile liners, fabric liners that are stapled into the bunker face and rest underneath the sand, are designed to hold sand in place, channel water into the drainage systems and prevent sand erosion, says Ted Fist, product manager for SandMat, a geotextile liner. Superintendents installing geotextile liners will have more labor costs during installation, he says, but will have less labor in putting bunkers back together after it rains.
“Our goal is to keep the water from crashing through the sand during an intense rainstorm and dislodging the substrate and contaminating the sand,” Fist says. “It keeps the drainage system cleaner and prevents catastrophic breakdowns that are hugely expensive to fix. The extra money they spend on installation on the front end will save them money down the road.”
Chuck Barber, superintendent at Indian Lakes Resort in Bloomingdale, Ill., sees the advantage to using geotextile fabrics as liners. He uses the SandMat 400. The bunker liners he uses keep the sand in place and improve drainage, a critical consideration in the Midwest where rains can sometimes wreak havoc with the sand in bunkers, he says.
“If you put the bunker liner into the face of your bunkers, you can create a direct channel into the drain tiles,” Barber says. “We have high-flashed bunkers, and we couldn’t keep sand on those slopes if we didn’t have bunker liners in place.”
Liners also help golf courses return the golf course to playability more quickly after a heavy rain, giving owners the opportunity to earn more money, Hutton says. “If you’re not having to send crews out to put the sand back into bunkers, they can be doing other things like squeegeeing greens or picking debris off fairways,” he says. “The amount you save on labor can be huge.”
Barber recommends choosing the proper staples to install the fabrics. Otherwise, freezing and thawing conditions can pull the staples out of the ground.
“If you’re going to use the geotextiles, you absolutely need to install the number of staples recommended by the manufacturer,” Hurdzan says. “I’ve seen superintendents scrimp on the number of staples and the amount of fabric they use. They always end up paying for it later.”
Superintendents will have to change the way they care for bunkers. “When you install a geotextile, it does require superintendents to groom the bunkers,” Fist adds.
Geotextile liners all but eliminate mechanical raking, Barber says. “You have to take into account the additional labor you will need so that you don’t tear or damage the liner,” he says. “But if you take care of the sand and the liner, you will save yourself money in the long run.”
Polyurethane. The first objection Bob McCormick, general manager of Klingstone, will hear about his product – a polyurethane bunker liner that binds the soil substrate together to prevent it from moving – is the cost.
“We understand going into a discussion with a superintendent that the first thing we’ll hear is that our system costs a lot more than other bunker liner systems,” McCormick says. “And it’s true. You will not get an instantaneous savings. But in the long run, you will save money.”
A spray-on polyurethane bunker liner costs superintendents about $1.20 per square foot to install, whereas a geotextile liner will cost anywhere from 20 cents to 50 cents per square foot (not including labor). But McCormick argues the extra costs are worth it because of the polyurethane’s durability and ease of installation.
Tim Johnson, superintendent of Spring Hill Golf Club in Wayzata, Minn., first installed Klingstone’s product in his bunkers 13 years ago during a renovation. He is currently the company’s longest-standing customer, and he says the extra cost up front is worth it.
“The only failures we’ve had are places where we didn’t install it properly in the first place,” Johnson says. “We decided to go with permanent liners because weather conditions here in Minnesota can get pretty nasty in the winter.”
Johnson doesn’t have to replace sand after a heavy rains because the polyurethane bunker liners do a solid job of channeling the water into the drainage systems. He adds it’s also a labor savings during the installation.
“It’s easy to install,” Johnson says. “You can send a two-man crew out to install it, and it’s no harder than spraying for weeds. Once you put it on, you’re good for the next 10 years.”
Johnson can’t stress strongly enough how important it is to calculate the proper rate of the product before installation. “You can’t skimp on the rate,” Johnson says. “You will have problems if you do.”
Sometimes it’s difficult to sell a greens committee or board of directors on the initial cost, so superintendents have to convince them to look down the road 10 or 15 years, Johnson says. The bottom-line for the product looks much better the further out you go, he says.
In the end, superintendents will have to decide for themselves if bunker liners are appropriate for their specific courses conditions, Hurdzan says.
“When superintendents do an in-depth cost analysis, they’ll discover that the most expensive part of the course to maintain is the bunkers,” Hurdzan says. “Anything superintendents can do to help bring down those costs is worth it.” GCI
Frank Andoraka Jr. is a freelance writer based in South Euclid, Ohio.
Liner Notes
Bunker work, like with any type of construction or renovation project at your facility, is a strategic financial investment meant to improve the playing experience for the golfer, as well as assist the superintendent and his team in their maintenance routine.
However, to fully realize the return on that investment it pays to do the project the right way, says Craig Porovne, vice president at Professional Turf Products.
Provone offers these liner notes to consider when embarking a bunker project.
• To accommodate cuts and waste, be sure to always add about 10 percent to your total square footage of liner.
• When determining sand, it's a sound practice to add an extra inch for depth because sand will invariably infiltrate the liner.
• Cover the entire bunker, drains, etc. Failure to do this will result in drainage gravel being mixed in with your sand.
• If you're covering the face of bunker and plan on laying sod on top of the liner, it makes sense to add 2-3 inches of soil and rub it into the liner for the turf's roots to take hold of.
• An important, an often overlooked, practice is to use Liquid Nails or another construction adhesive on all seams.
• Most importantly, if you're hiring a contractor to do the work, then make sure he is a certified builder from the GCBAA list.
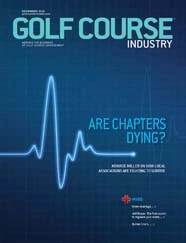
Explore the December 2010 Issue
Check out more from this issue and find your next story to read.
Latest from Golf Course Industry
- Golf Construction Conversations: Reed Anderson
- ’Twas the Night Before Christmas (on turf)
- Twas the Night Before Christmas (the turf version audio)
- Advanced Turf Solutions and The Aquatrols Company release soil surfactant
- Heritage Golf Group acquires North Carolina courses
- Editor’s notebook: Green Start Academy 2024
- USGA focuses on inclusion, sustainability in 2024
- Greens with Envy 65: Carolina on our mind