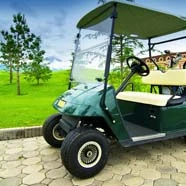
Back in 2004, I wrote about cart path design, and that it is only half the equation in a successful cart path project. Many courses add paths each year, with bad results and poor construction. With today’s cost-cutting culture, I suspect more cart path projects will be done in-house and with low-cost contractors. So, I offer some thoughts on building cart paths correctly. As with all the other generalized advice, this column is no substitute for determining a program based on your site-specific conditions, but covers the most typical problems I have seen.
REINFORCEMENT. Most cart paths are built using only “fiber mesh” reinforcement, usually for speed and cost reasons, whereas most concrete work is reinforced with wire mesh or re-bars.
Fiber mesh increases tensile strength and controls hairline cracks caused by shrinkage. However, finishing can be harder to do well, and it’s a non-load bearing surface. If you are using only fiber mesh, you should consider increasing pavement depth from 4 inches to 4.5-5 inches.
You need more reinforcement if you have expansive clay soils, slopes over 5 percent or extreme temperature variances. You may also have a few areas carrying heavier loads – often near the maintenance area – that require extra reinforcement. Most specs call for the reinforcement in the vertical center of the pavement, but setting and keeping the mesh or re-bars within ¾-1 inch of the top surface, during concrete pouring, is the only way to get any benefit in crack control.
EXPANSION and CONTRACTION JOINTS . Approximately ½-inch wide wood or rubberized expansion joints are required adjacent to any structural elements, and along the path. There is a formula that varies with temperature extremes and soils, but maximum spacing is 80 feet. Contraction joints sawed partly through the concrete are placed even more frequently to control cracking, with a good rule of thumb being to place 5/8-inch-wide joints at the lesser of 1.5 times either the width of your pavement (12 feet apart for an 8-foot-wide path) or the depth of your pavement (6 feet apart for 4-inch-deep concrete). And in bigger areas, like turnaround circles, you must have them at no more than 180 degree angles to prevent cracking pavement.
SUB-BASE. The best base material is usually to cut the path into native soils, with no sand or aggregate leveling course required. Just don’t cut so deep as to leave drainage problems and compact to 95 percent standard proctor density – which is usually easy to attain with rollers. Import fill used to raise the base must be similar soil material or you will have different shrink/swell conditions which lead to cracking. Gently wetting the sub base prior to installation achieves optimum soil moisture and minimizes cracking down the road.
MATERIAL PROFILE. Most cart paths are 3000 psi concrete strength. I specify six-sack rather than five-sack concrete mixtures, which often yields over 4000 psi. The additional 20 percent concrete cost yields another 33 percent of strength and is a good value. It’s also becoming more common to use fly ash as 10-15 percent of the cement mixture, which reduces heat in the hydration process, is cheaper and produces a harder, denser surface.
Each project should have a unique concrete mix, so there are other concrete components to be aware of. For example, site conditions sometimes require use of air entraining, water reducing to achieve a lower water-to-cement ratio for greater strength using less cement and retardants or accelerants to slow/speed drying in hot/cold weather.
You will also need to consider extras like colorants, sealants and textural finishing to attain your desired results.
KNOWING MORE THAN THE CONTRACTOR. Its imperative you know all of the above and more and that the contractor knows you know it. Testing and inspection is the key to quality work. You will need periodic samples tested as they come from the plant, and there are many in field tests, like slump tests, that will verify you get the concrete you specified. Be diligent. In cart path construction you don’t get what you expect, you get what you inspect! GCI
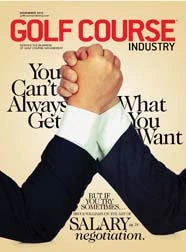
Explore the November 2010 Issue
Check out more from this issue and find your next story to read.
Latest from Golf Course Industry
- Golf Construction Conversations: Reed Anderson
- ’Twas the Night Before Christmas (on turf)
- Twas the Night Before Christmas (the turf version audio)
- Advanced Turf Solutions and The Aquatrols Company release soil surfactant
- Heritage Golf Group acquires North Carolina courses
- Editor’s notebook: Green Start Academy 2024
- USGA focuses on inclusion, sustainability in 2024
- Greens with Envy 65: Carolina on our mind