Self-Contained Topdressing Brush
Ken Williams, CGCS, at the Stanford University Golf Course and Seibel Varsity Golf Training Complex in Stanford, Calif., enjoys using the Standard Golf Model #52000 topdressing brush, with two Model #52050 wing brushes, mounted on the back of a 1985 Toro Model #8880 Sand Pro. Tom Thatcher, the former superintendent who is enjoying retirement, developed the idea for the brackets that are two pieces of 2-inch angle iron welded to the lift bar, with two pieces of 1-inch-wide by 1/8-inch-thick flat steel that is screwed to the two 2x4x24-inch boards along with a flat-steel cross brace of the same dimensions.
There are three 1½-inch chains attached to the lift arm that lift the main topdressing brush. The boards have two pieces of ¼-inch diameter yellow nylon rope tied to it and to both of the wing brushes, with eye hooks, so when the lift arm raises the main brush it raises the wing brushes at the same time. The two wing brushes fold up efficiently and easily for transport. The Toro Sand Pro was outfitted with 21x12x8-inch slick tires available from www.Tires-Easy.com. It took roughly two hours total to design, and about four hours to build and the materials were already in stock.
The Windmeister
Brad Chutz, co-owner/superintendent of the Pine Grove Golf Course in Grove City, Pa., challenged his crew to find a better and faster method for removing leaves from the greens and tees. The method they always used was a backpack blower and a three-wheeled, push-type blower which would take hours. To speed up the process, they took an old Toro Sand-Pro with Carlisle 22/1100/8 four-ply turf tires, left the two lifting arms for the rakes in place and drilled two holes ½ inch in diameter in each lifting arm. They then took a piece of ¼-inch-thick, 10x26-inch steel plate and drilled four ½-inch-diameter holes to match the holes in the lifting arms, then bolted the ¼-inch plate to the lifting arms. Next, they took a three-wheeled 1997 Giant Vac walk-behind push blower ($900 new) and removed the rear wheels leaving the axle in place and the handle bars were removed. The blower was set on the plate, two pieces of 1½-inch angle iron 2 inches long were welded to the plate to set the axles onto and using the engine mounting bolt holes that were used to hold the handle bars in place, and four holes were drilled through the steel plate on that location. With the axles setting in the “V” formed by the angle iron, the bottom of the engine for the blower was 4 inches above the plate. Using ½-inch-diameter pipe, four spacers 4 inches long were cut and the spacers were used to mount the blower to the plate with four 3/8x16x5 bolts.
The throttle for the engine was mounted on a bracket under the seat so the operator could control the throttle of the blower without having to get off the unit. The third wheel was left in place on the blower to prevent lowering the blower too far and damaging the turf. With the assembly mounted to the Sand-Pro lift bars, the height of the blower can now be controlled with the hydraulics to be raised or lowered for transport and blowing. This modification has turned a two-person job that would take up to four hours into a one-person job that takes about an hour. The cost was about $60 and it took about three hours to complete.
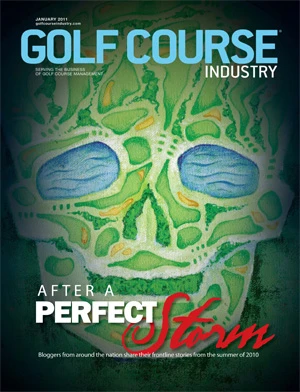
Explore the January 2011 Issue
Check out more from this issue and find your next story to read.
Latest from Golf Course Industry
- Toro continues support of National Mayor’s Challenge for Water Conservation
- A different kind of long distance
- Golf Construction Conversations: Stephen Hope
- EnP welcomes new sales manager
- DLF opening centers in Oregon, Ontario
- Buffalo Turbine unveils battery-powered debris blower
- Beyond the Page 66: Keep looking up
- SePRO hires new technical specialist