There is no shortage of stories about the recent struggles of the golf industry amid a global economic meltdown – including course closures quickly outpacing new course openings. Rounds played are down, superintendents and golf professionals are being laid off, and golf course homes continue to devalue as some courses close their doors for good. But rather than dwell on the negative for yet another disheartening story, why not focus on one of the bright spots in the golf course design and construction business: the Cypress Tree (West) Golf Course at Maxwell Air Force Base in Montgomery, Ala.
A decade before the economy ground to a near standstill, stimuli came packaged for mass consumption, and taxpayers each owned a little slice of GM, the US Air Force began the due diligence of a study in conjunction with the USGA to determine which base golf courses were most in need of repair with the goal being long-term savings and generating revenue. After years of study, courses in Ohio and Florida were tapped to go under the knife, followed by Bay Breeze Golf Course at Keesler AFB in Biloxi, Miss., and then Cypress Tree.
Cypress Tree is a case study in what is possible with the right project team – owner, architect, builder, and golf course staff – and carefully detailed planning. When our firm was selected to handle the design of the Cypress Tree project, we were still finishing the Bay Breeze project in Biloxi. The scope of work for the two projects was similar in nature: the focus was on improving greens and bunkers using “repair by replacement to current industry standards.” However, the funding for Cypress Tree was considerably less – about $650,000 to renovate 19 green complexes, greenside bunkers, irrigation green loops, sprigs and sod – with constraints on maximum aggregate and individual green sizes, the number of bunkers and one last thing – it all had to be completed Maxwell AFB, No. 13, before renovation.and grassed in 16 weeks before the fiscal year ran out.
While a number of “signature” architects have recently discussed being forced to take on much smaller projects to keep their staffs busy, over the last 15-plus years of my career I have been no stranger to tight construction budgets and felt as though our firm was up to the task. We have built a reputation for our firm by squeezing $1.25 out of every $1 we have been budgeted and we have yet to be given carte blanche on any project. I knew the Cypress Tree project would work if we could establish two critical points up front. First, we would have to build the new greens to “California” greens specifications instead of USGA specs. The Air Force allows for using this construction method and I had designed a number of renovation projects in the recent past using variations of this method as a means of cutting cost without cutting quality.
Secondly, we would have to provide the contractor and myself with more flexibility not only in the design, but also in the construction methodology to be utilized and timing of the schedule. Before we came on board, the prevailing thought regarding the project for some at the Air Force was to simply core out the existing greens and rebuild them to USGA specifications using the existing contours, install new irrigation green loops, and “re-dress” the bunker faces and install new sand – all done without disturbing any areas between the greens and bunkers. Given my experience with similar projects – and as the Maxwell AFB, No. 13, after renovation.son of a lifelong general contractor – my gut instinct was that forcing a contractor to dance around nineteen green cores and nearly thirty separate bunkers would require a tremendous amount of hand labor and headache for the contractor, thus adding additional cost to the project.
Additionally, the base would not allow stockpiling of the material so the contractor would be required to haul the cored out material off base, adding a tremendous amount of hauling cost and damage to the rest of the course. Conversely, my solution was to treat each green complex as nineteen separate yet interconnected work sites. We would use the material from each existing green to build the new surrounds and bunkers in that complex, eliminating the cost of hauling off material and providing much needed fill for creating the mounding and contours I felt were necessary. As a result, my design called for the complete razing and re-shaping of each green complex to create a newly-designed green and bunkers – we could have neither more nor fewer total bunkers than we found on the existing course, though we could move the bunkers between holes if needed. This enabled the contractor to move a small dozer and shaper into a green complex and work within the limit of work without having to dance around dozens of areas that were off limits and smoothly transition the new bunkers, greens, and mounds into the surrounding topography to produce a natural and appealing finished look. While some degree of hand labor on every course may be inevitable, I have long held that the end result of one of my renovation projects should be the reduction – and not the increase – of the cost of subsequent daily maintenance. To that end, my bunker design style calls for semi-flat bottoms and sodded faces. This not only eliminates a good deal of hand labor from raking up flashed faces, but it also does not require expensive bunker matting material to be installed. The old bunkers on the West course were eyesores typical of their day which held water after a rain and were costly to maintain. Allowing us to treat the entire green complex as one single work area enable us to remedy that problem while transitioning into the green surfaces seamlessly.
Lastly, the timing of the project was critical. With time running out to complete the project, I put the project out for bid in late summer with the construction start date set for Jan. 2. I knew some golf course contractors in the Southeast would be wrapping up projects at that time and looking for projects for the coming year. Even though the contractor would only have 16 weeks to finish the project, I hoped securing a contract early before contractors began really chasing projects for the coming year, we could nail down a better price. The gamble paid off. Not only did we secure a bid within our tight budget number, but we also did so with one of the country’s most respected golf course contractors.
I cannot say enough about the project team members for the project who each enabled the work to be completed in just four months and within budget. Golf course superintendent Glenn McWhirter and his staff did a tremendous job of aiding me in monitoring construction and growing-in the course before opening day. The Air Force Center for Engineering and the Environment (AFCEE) based in San Antonio served as the USAF representative for the project and Contracting Officer, working closely with me in the administration of the project from conception to completion, and kept the project moving forward despite the typical unforeseen circumstances that those in our line of work run into on nearly every renovation project. The general contractor and golf course contractor – Texas-based E2M, and Nebraska-based Landscapes Unlimited – were superb in the professionalism and quality of their work and the finished project looks like we had a budget twice as large as the actual budget.
The project at Cypress Tree proves that opportunities still exist for moderately-priced renovation to existing courses even in these economic times with the proper planning and the right project team. There may be far fewer new courses opening these days, but existing courses cannot be allowed to become stagnant and rest on their laurels waiting for things to get better. Clubs and public course must be proactive because there are still core golfers who play regularly and are shopping for better value and opportunity.
This could prove to be an excellent time for you to invest in carefully-planned and conservatively-funded capital improvement plans at your course that may prove to be the difference between struggling financially or attracting new golfers from other facilities that are forced to cut back. Some projects such as bunker renovations, improving green complexes, or upgrading your irrigation will actually be a cost savings in daily operations with a quick return on investment, and the right improvements attract the golfers who will help to pad your bottom line – thus preventing continued budget cuts, layoffs, and the defection of members for private facilities and players for public courses. Instead of asking “Can we afford renovations right now?” perhaps the better question really is “Can we afford not to look at renovations?” GCI
Nathan Crace is the principal at Watermark Golf/Nathan Crace Design.
Get curated news on YOUR industry.
Enter your email to receive our newsletters.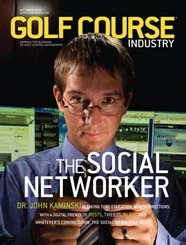
Explore the October 2010 Issue
Check out more from this issue and find your next story to read.
Latest from Golf Course Industry
- Advanced Turf Solutions’ Scott Lund expands role
- South Carolina’s Tidewater Golf Club completes renovation project
- SePRO to host webinar on plant growth regulators
- Turfco introduces riding applicator
- From the publisher’s pen: The golf guilt trip
- Bob Farren lands Carolinas GCSA highest honor
- Architect Brian Curley breaks ground on new First Tee venue
- Turfco unveils new fairway topdresser and material handler