At the heart of every irrigation system beats the pump station. And from that heart flows water – the lifeblood of turf and landscape plants.
For every golf course there are several distinctive requirements – and opportunities – for creating the optimal pumping system. Water sources, power availability, operating window, design hydraulics, emission choices and more determine capacity needs and restrictions around which to actually design a pump station.
Review the technology
Background information is always helpful when facing a pump station rebuild or replacement – or when increasing the performance of your existing system. Four basic types of pumps can be used in design to deliver the tremendous range of flows and pressures demanded by modern golf courses and country clubs:
- Centrifugal pumps used for surface or ground water sources are primary water suppliers (transfer pumps). Centrifugal pumps can lift water, but suction/lift capacities vary, usually ± 10-foot maximum. This brings obvious limitations, along with reduced efficiency, and therefore is not common in today’s systems.
- Centrifugal pumps with positive suction pressure are used as surface water boosters – most common in the boost of a water tank or city supply. These systems can be both constant-speed and VFD controlled.
- Vertical turbine pumps also are used as primary water suppliers, moving water from lakes, rivers or wells into irrigation systems. These pumps are most prevalent – often using multiple stages – and can run at lower RPMs. They are most common in today’s systems, and when coupled with VFD controls, are the most efficient means of water delivery today.
- Submersible pumps, too, are used as primary suppliers, moving water from lakes, wells or rivers. Trash pumps could fall into this category as well, and are mostly used to transfer water. Said pumps have high initial costs and generally low efficiencies.
Assess resources and goals
Pumps with a high efficiency at minimal flow rates obviously cost less to operate. Constant speed systems that utilize multiple pumps of various sizes are moderately efficient, while variable-speed drives (VFD) use fewer but larger pumps and enable the fluctuation of pump speed to match any oscillating flow requirements, thus producing the highest level of efficiency. Today, as costs go down and efficiency rates go up, about 90 percent of golf controls are VFD coupled with turbine stations. Of all the different combinations of controls and pumps, this is the most efficient for pressurized irrigation.
Assemble your team
No single assortment of pumps and controls suits every application, nor is there a single manufacturer that can meet every customer’s needs. Your type of source water and water quality should ultimately determine the optimum combination of necessary equipment. Because each golf course is one of a kind, engineering the perfect pump station takes a team. Those responsible for system cost, design, installation, operation and maintenance must contribute to make the best station selection. This includes owners and consultants, superintendents and irrigation technicians, certified manufacturer technicians/contractors and manufacturers.
There’s a long list of considerations in engineering an efficient, durable pump station. Begin your quest with a strong knowledge of your site, sources and personnel. Formulate the necessary support team and ensure that all consultants, distributors and representatives speak your language. GCI
Get curated news on YOUR industry.
Enter your email to receive our newsletters.
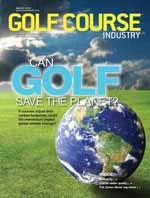
Explore the March 2010 Issue
Check out more from this issue and find your next story to read.
Latest from Golf Course Industry
- The Cabot Collection announces move into course management
- Carolinas GCSA raises nearly $300,000 for research
- Advanced Turf Solutions’ Scott Lund expands role
- South Carolina’s Tidewater Golf Club completes renovation project
- SePRO to host webinar on plant growth regulators
- Turfco introduces riding applicator
- From the publisher’s pen: The golf guilt trip
- Bob Farren lands Carolinas GCSA highest honor