Inexperienced in certain areas, a team develops a distinct course in the Phoenix Valley
There were a couple of firsts involved with the development of the Blackstone Course at Blackstone Country Club in Peoria, Ariz. Golf course architect Jim Engh had never designed a golf course in the desert. Golf course superintendent Roger Brashear had never been the lead golf course superintendent during a grow-in. However, the experience of Denver-based American Civil Contractors and the fact that the company builds many of the courses Engh designs helped the project progress smoothly. Those involved say it turned out beautifully.
Out of the gate
Sunbelt Holdings, which partnered with Shea Homes to develop Blackstone, studied the marketplace diligently, says Mark Hammons, vice president of Sunbelt.
“With the entitlement we have, we’re able to build five golf courses,” he says. “We already built a public golf course and wanted to build a private one. We think we’ve created something that’s not found in this valley with production homes, custom homes and a golf course.”
Hammons says there aren’t many golf clubs in the area at the Blackstone’s price point, which is $60,000 for a club membership. He says Arrowhead Country Club is probably the closest club in price to Blackstone, but it’s an older facility. Quintero Country Club, about 20 miles northwest of Blackstone, is at the high end of the market.
“Those are the two extremes, and there was nothing in the middle,” he says. “Blackstone is a home club. We are building custom homes for empty nesters and young people.”
Moving forward with the golf course project, Sunbelt interviewed Engh and liked his philosophy of working within what the land presents.
Before working at Blackstone, Brashear was superintendent of the Cochise Course at Desert Mountain for about four years. He heard about Blackstone through Intrawest Golf Management, which had contacted him about working at one of golf courses it manages, including one in Vistancia near the Blackstone site. Those courses didn’t interest him, however, Brashear was interested in the Blackstone project because he had never been the lead superintendent during a grow-in and was excited to stay in Arizona.
Rick Maher, operations manager for ACC Golf, an arm of ACC, says the company was interested in the project for three reasons: (1.) Engh, with whom it had a good relationship, designed the course; (2.) working in Arizona in the winter is preferable; and (3.) Shea Homes and Sunbelt are big clients.
Design style
Sunbelt’s management team, which includes several accomplished golfers, looked at the land and thought it would be developed into a normal desert golf course with carries, elevation changes, boulders and landscape creations.
“But when the management team started talking to Jim, and he said he had never done a golf course in the desert, management then said, ‘We want something different,’” Hammons says. “There’s criticism that a lot of golf courses out here are similar, but with Jim, the links style, greens design and bunkers (there are only 30 of them compared to 60 or 70 on a typical desert course) are different. He makes playing the course challenging but rewards you for thinking through the round. If you hit an errant shot, but get the distance right, you have the opportunity to make par.”
Engh incorporated many natural features in his design. For example, there’s a natural land berm blended into the eighth hole, and a green tucked in a cove surrounded by natural earth on the ninth. The site features many arroyos and drainage areas that Engh could capitalize on, allowing him to bring his style to the desert.
“I have a love for Ireland and using the land as it is, although I’m not afraid of creating things where nothing exists,” he says. “I don’t want repetition on the golf course.”
Engh worked well within the land, which is part of his style, Hammons says.
“We moved between 200,000 and 250,000 cubic yards of dirt,” he says. “It was kind of a clean slate in terms of the land and design, except for the 404 (permit) areas that run through the site.”
On the site, 404 areas are dry streambeds deemed wetlands by the Army Corps of Engineers that can’t be disturbed.
Other than the 404 areas, which were a constraint when designing the course, Engh says he was able to route the course where he wanted to. The 404 areas determined where some holes went. Some holes touched nothing and fit perfectly. Other holes were different. For example, Engh chose a flat area to put an irrigation pond and one hole wrapped around it with an Irish flair.
“We went through a selection process, so the owners knew the look they would get with us, and that allowed us to move forward without much interference,” Engh says.
Being a desert course, a maximum number of acres of maintained turf – 90 – is part of the construction equation.
“We have really big landing areas, but there’s no grassing around the tees and up to the fairways,” Engh says. “The course is 7,089 yards from the tips, but additional length wouldn’t change the number of maintained acres of turf. I design for a scratch player. The challenge is designing for the Tour players. For me, I cover 99 percent of golfers by designing for the scratch golfer.
“I became more bold and confident by understanding that one out of every five golfers won’t like the layout, and that one person will be the most vocal,” he adds.
Engh and Hammons prefer when a golf course superintendent is on site from day one, and Engh likes the superintendent to lay out the irrigation system. Brashear was there for that.
“He reviewed Jim’s plans and offered suggestions from a maintenance standpoint,” Hammons says. “It was a great advantage to have Roger on that early.”
Builder relations
Building in the desert can be tricky. Anything that’s disturbed won’t grow back, Maher says.
“We take the time and effort not to tear up any more than we have to,” he says. “We’re focused on minimal disturbance.”
Other than running into hard ground and working in 110-degree temperatures, everything went smoothly, Maher says.
Engh was on site periodically, but during the shaping process and grassing, he was there more often. During construction, there weren’t many change orders, Engh says.
“When we hit rock, there were change orders that needed to be made,” he says. “We also added a few irrigation heads here and there.”
Potential issues were addressed before they became problems, Maher says.
“Roger is the more-than-helpful type,” he says. “He was there to solve problems, not create them.”
Working with ACC was a positive experience for Hammons.
“They wanted to come to this market, so they were aggressive with their price,” he says. “We were adamant about keeping the disturbance to the landscape outside the golf course to a minimum. They met the timeline. They held to their numbers. ACC knew Jim and his philosophy so there weren’t many change orders, but there were many small changes that were absorbed in their daily operations.”
Brashear also was pleased to work with ACC.
“We learned a lot from each other,” he says. “Being my first golf course build, I was scared so bad because you have to do it right. It was up to ACC and me to make it happen.”
Because the course is part of a master-planned community, it will be surrounded by homes eventually. But, as of mid-September, none of the homes had been built yet, but lots have been sold.
Water supply
Water is always a concern when building a golf course, especially in the desert. Engh says the water set-up and delivery was already resolved before he arrived, which allowed him to focus strictly on the golf course. Sunbelt worked with the city of Peoria and the Central Arizona Project, a water provider. The property on which Blackstone sits is bisected by the CAP canal, which channels water from the Colorado River. Additionally, Blackstone has a wastewater plant that provides Class A effluent water.
“We have two lakes with effluent water, and we will we wean ourselves off of the CAP as soon as possible, as we build more homes,” Hammons says. “Out of every 100 gallons that goes into the treatment plant, 80 percent can be regained to go back into the golf course’s irrigation system. We will spend more than $15 million in the wastewater treatment plant.”
Selection and care
When building some courses, depending on location, the choice of what grasses to use can be daunting. But not for the Blackstone project. 419 Bermudagrass was used on the tees and fairways, and Tifeagle Bermudagrass was used on the greens. The varieties are typical grasses in the desert because they’re durable and stand up to the weather. Because the greens’ design and the weather, it would be difficult to grow bentgrass, Brashear says. There wasn’t a lot of choice with the grass because of the greens’ design and the desert location.
“We toyed with the idea of bentgrass greens but because of the heat, we decided it wasn’t prudent,” Engh says.
Brashear says Tifeagle makes for a perfect putting surface if it’s verticut and topdressed regularly. He grooms the greens four times a week, verticuts once a week and brushes twice a week.
“Tifeagle is known for thatch, but if you don’t deal with it every day you’ll have problems.”
The Blackstone project started late in 2003, and sprigging finished in September of 2004. Hammons says Sunbelt missed its marketing window but ended up with a year-and-a-half grow-in. The course, which is overseeded with ryegrass in the winter, is going through its first year of transition.
“Until we sell every house around here, we’ll overseed,” Brashear says. “There are a lot of benefits to not overseeding, but I understand why they want to do it.”
Brashear says it takes a lot to maintain the course. For example, there’s a lot of hand work needed around the bunkers because they’re severe.
“As Jim once said, this course won’t be low maintenance, but I’m 34 and am not looking for an easy course to maintain,” he says. “When I’m 70 and still doing this, I’ll be looking for the flattest course in Kansas. The course is hard to maintain, but it’s fun. I haven’t found anything to complain about. There are a few areas of the course that take more to maintain, but it’s beautiful.”
That’s entertainment
Of the 20-plus projects Engh has worked on since starting his own firm in 1991, he says the desert setting makes this course stand out. A lot of roll into the greens, flat areas around those rolls, and several ways to look at shots onto the greens are a few of the aspects that differentiate Blackstone from other courses in the area.
“We brought our vision into a desert setting,” he says. “It’s a golf course that looks like nothing else in the Phoenix Valley. There’s a wide variety of randomness. You can play it 30 times, and still not figure it out. We’re bold with our individual hole characteristics.
“We’re in the entertainment business,” he adds. “If you look at it any other way, you’re missing a large part of the business.” GCN
At a glance
The Blackstone Course at Blackstone Country Club in Peoria, Ariz.
Owner: Sun Belt Holdings and Shea Homes
Architect: Jim Engh
Builder: American Civil Contractors
Golf course superintendent: Roger Brashear
Cost to build: $9 million
Length: 7,089 yards
Par: 72
Number of holes: 18
Project started: Fourth quarter of 2003
Course opened: Fourth quarter of 2005
Turfgrass on greens: Tifeagle Bermudagrass
Turfgrass on tees and fairways:
419 Bermudagrass
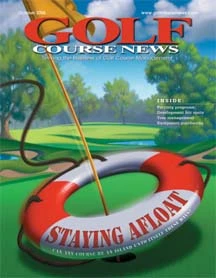
Explore the October 2006 Issue
Check out more from this issue and find your next story to read.
Latest from Golf Course Industry
- The Cabot Collection announces move into course management
- Carolinas GCSA raises nearly $300,000 for research
- Advanced Turf Solutions’ Scott Lund expands role
- South Carolina’s Tidewater Golf Club completes renovation project
- SePRO to host webinar on plant growth regulators
- Turfco introduces riding applicator
- From the publisher’s pen: The golf guilt trip
- Bob Farren lands Carolinas GCSA highest honor