
The Titans, born of Sky and Earth, ruled the world until they were overthrown by the Olympian deities, led by Zeus with his powerful master thunderbolt. Technician titans still exist and, using all their talent, make the seemingly impossible possible. A worthy technician will save the day with exceptional ability and by contributing to a culture that is respectful and productive. Often caught in a stormy gray area between superintendents and assistants, the transformative powers of a leading technician are something every crew needs.
Talent and teams
At Medinah Country Club in suburban Chicago, there are three courses (Nos. 1, 2 and 3). Course 3 has hosted three U.S. Opens, two PGA Championships and the 2012 Ryder Cup. Across the entire property they roll out $1 million to $2 million of inventory every day. “We have few if any breakdowns,” says Steve Cook, director of grounds operations. “We have a very good mechanic staff. They’re tuned into play and what the expectations are on the golf course. They know how preparing for play is important and how they’re a key part of that. They are the key part of it, actually.”
Brian Bressler, Medinah’s equipment/shop manager, leads a team of three fulltime technicians (one recently hired) and four seasonal staff, which includes two additional technicians and two shop stewards. One shop steward is responsible for everything inside and the other takes care of the yard. Seasonal employees are recruited in the same manner as turf interns and they come from mechanical schools across the country. Medinah employees are developing a good relationship with a nearby school and are actively working to establish a mechanical recruiting pipeline.
Cook spent more than 20 years at Oakland Hills Country Club in suburban Detroit before moving to Medinah in April 2018. He says there has been some turnover in the past 18 months, but things are going well. Cook is especially pleased with the progress in the shop. “Hopefully, it is something we can manage like the turf side,” he says. “We bring new people in, train them and help place them in their next role.” Working at this highly regarded venue is a key benefit of the job and they have already placed one mechanic in the Chicago area.
Robert Nichols, equipment manager and assistant superintendent at Willow Brook Country Club in Tyler, Texas, would agree that training is important, as is being appreciated. “One big issue with techs is that they get caught between assistant superintendent and superintendent,” he says. “Assistants come and go, but techs can be long-term. I would encourage supers to keep their techs happy. Give your tech the raise and praise they deserve. Training is a big factor.”
Both Medinah and Willow Brook have a prestigious membership with high expectations, were established in the early 1920s and have a rich golf history. Willow Brook has a newly-renovated 18 holes, two putting greens, a practice hole, two driving range tees and a four-hole short course designed to teach children the game of golf.
There is plenty to care for and Nichols spends a “typical” week working Monday through Saturday from 5:30 a.m. until about 4 p.m. He stages equipment, checks the cut quality on turf and checks green speeds for consistency. He helps with verticut and aerification setup and operation, grinds reels as necessary, services and repairs equipment, and checks the course for damage. Saturdays are for picking up sticks, blowing pine needles and servicing greens mowers plus many, many other responsibilities.
Being a technician is busy and Cook and Nichols both note that low pay is problem. “What is affecting how many people are interested in the job is money,” Cook says. “We require techs and if you are recruiting from the construction industry, heavy equipment, auto, trucking or wherever, you have to be competitive if you want a good one.”
Techs can start with salaries in the low $20,000s, but that will grow to six figures for the best. That’s a huge range and one recruiting tool is to show candidates a clear path to better pay, a promotion or both. Get recruits engaged and interested from the start whether you plan to retain them at your property or help them move up the ladder to receive a promotion elsewhere.
“The first thing I stress to young techs is that simple service is your best friend,” Nichols says. “Changing oil and greasing is paramount. Pull out and put away all equipment to make sure it starts, runs and is safe for use. Machines and buildings have issues from time to time, that is a fact. Getting upset doesn’t help and if it bothers you when things break, you’re in the wrong profession. Be organized with your maintenance routines.”
There must be a component of continuing education. “Tech, superintendent, turf and equipment sites all help do the job,” says Nichols, and he also stays current with Environmental Protection Agency regulation changes. Learning about on-board diagnostics 1 & 2 are a must and emission controls are “here to stay.” Nichols shares that the Willow Brook staff is fantastic and one of the best parts of his job is helping the staff exceed all expectations.

Cultivating the culture
At work, exceeding the expectations of the members — and each other — is possible when employees understand those expectations and hold each other accountable. At Medinah, one expectation is for the equipment to be in great shape. If something needs to be fixed, it gets fixed. “The equipment and people in the shop are the most important part of any golf course operation,” Cook says. “I can do what the assistant does, but I can’t do what the technician does. It’s the same for training.”
With a little more than a year between starting in his new role and hosting the BMW Championship in August 2019, Cook says he “slowed everything down. We governed the equipment down, some of it to 1 mph, so the staff could understand the importance of respecting it. Staff get frustrated when the equipment isn’t working and that can start a downward spiral of apathy. So we slowed down and started washing equipment routinely. People had to adjust to a culture of caring for an inventory of $5 million of equipment that somebody else paid for. We are still driving tractors in first gear. After three seasons, we’re ready to loosen up for greater productivity.”
Medinah also put about $300,000 into renovating the maintenance facility “to show respect to the technicians who occupy that space and to show the staff and members that equipment maintenance is important,” Cook says. The staff are now more cognizant of the equipment and why it is important to get the culture right. The budget for fixing equipment isn’t unlimited, but it’s fluid. Equipment is required for the job.
Bressler notes that it’s important to have good service from your distributor and the best way to keep staff up to speed is “training, training, training, everything from how to use it to what it is used for and how to keep it clean and maintained properly.”
Of utmost importance is the quality of cut and the team is “pretty dialed in on that,” Cook says. “One mechanic will go out on each golf course, each morning, and check all the mowers for quality of cut. They also check soil temperatures and surface temperatures. They are part of the mowing team to make sure that everything goes smoothly.”
Alongside the morning mowing routine, Bressler has developed a maintenance system that works for Medinah. He has set up the shop to be as digital as possible. All the technicians have a 10-inch tablet and the operating manuals are on a Google Drive in a shared folder. The agronomy team can access these manuals from the course, and for everyone, being able to access manuals without traipsing to a central location saves a lot of time.
Google Drive also houses logs for repairs and servicing. Bressler has created Google forms and every piece of equipment has a QR Code. “When we’re working on a piece of equipment, it has an ID tag on it that has the make, model, serial number, year and its QR Code,” he says. “We scan the code and it takes us to the manual(s) for that machine. We can troubleshoot quickly.” Another benefit to this system is that it’s free and there is plenty of storage space. Finding a reliable, easy-to-use system that works for your tech crew is paramount to implementing a respectful culture where everyone consistently knows what to expect.
Bressler participates in meetings and the maintenance staff is part of manufacturer demonstrations. The technicians will care for the equipment so they need to be part of the process from the start. Medinah hasn’t found any autonomous solutions that fit its needs, but they are open to anything new.
As you evaluate the efficiency of your program, what kinds of techs are ideal for your organization? There are many different types: irrigation, cart, spray, equipment, repair and the list of titles continues. Concentrate on the mix of techs who will work for you. Are language barriers causing a problem? Different terminology used among generations needs to be worked through, but if multiple languages are spoken in the shop, is it possible to have manuals accessible in multiple languages? Also, is all the equipment suitable for people of different sizes? For instance, can all of your machines be adjusted for the tall and the small? If not, is there a safe way to fix this, or a way to assign equipment in a way that everyone can work in the most ergonomic way possible? Considerate details make a difference.
Though the Titans faded out of popularity long ago, the technicians never will. It’s paramount they are respected in the way they should be, given the chance for raises and promotions, and can work their way through a career that is fulfilling. A powerful technician can transform your operation — and that’s not a myth.
“I have always put a big focus on the equipment repairs, on the shop and on the shop yard,” Cook says. “You have to take care of your house first and everything else will fall into line.”
Get curated news on YOUR industry.
Enter your email to receive our newsletters.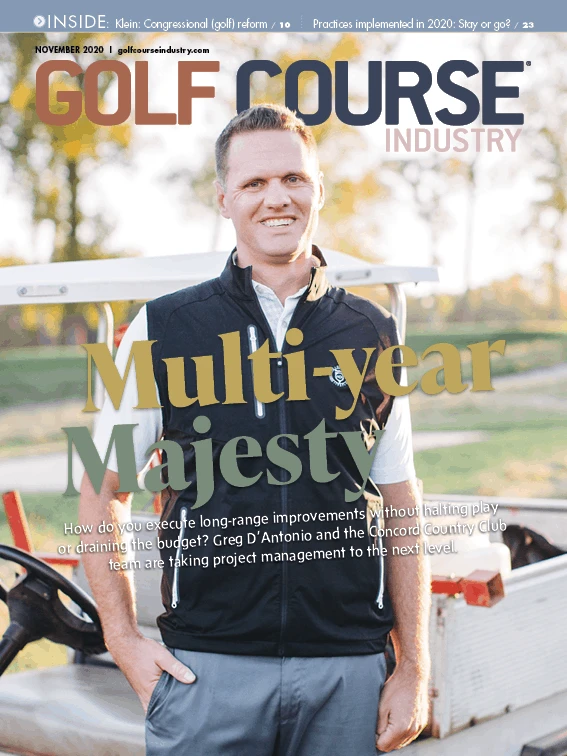
Explore the November 2020 Issue
Check out more from this issue and find your next story to read.
Latest from Golf Course Industry
- Carolinas GCSA raises nearly $300,000 for research
- Advanced Turf Solutions’ Scott Lund expands role
- South Carolina’s Tidewater Golf Club completes renovation project
- SePRO to host webinar on plant growth regulators
- Turfco introduces riding applicator
- From the publisher’s pen: The golf guilt trip
- Bob Farren lands Carolinas GCSA highest honor
- Architect Brian Curley breaks ground on new First Tee venue