Hold the ladder
Equipment manager Gary Slaughter and Jed Spencer, CGCS, designed and built a ladder holder for the 1998 Club Car Carryall II equipment manager’s vehicle at the Chenal Country Club in Little Rock, Ark.The ladder holder is made of 1-inch by 1-inch, thin-wall (-inch thick) square tubing that has two vertical supports at 40-inches high each. The supports are 44 ¾ inches apart, 25 inches wide over the top of the canopy with two 6-inch long vertical brackets that support the ladder. Cross braces provide added support.
The ladder holder is attached to the turf vehicle’s canopy uprights with ¼-inch diameter bolts, washers and nuts; ½-inch spacers are used in between the ladder holder and windshield so the windshield can be opened or closed. An 8-foot long aluminum ladder is transported permanently where one side of the ladder is placed in between the two 6-inch long vertical brackets. A 20-foot fiberglass extension ladder also can be transported with ease. It took about two hours to design, cut and weld the ladder holder. The materials cost about $30.
Spreading in style
At the Great Southwest Golf Club in Grand Prairie, Texas, equipment manager Jeff Jamnik designed and built a 12-volt fertilizer spreader. He attached a Lesco #80 Electric Truckster Commercial Plus Spreader to a 2005 E-Z-Go MPT 1200 G turf vehicle with a 2-inch square tubing (-inch thick) frame. The frame is 27 inches high and the section that goes into the receiver is 18 ½ inches long and has a triangular-shaped brace were all pieces are welded together. Jamnik painted the brace with three coats of glossy black enamel.
The spreader is mounted to a 21-inch by 4-inch (¼-inch thick) piece of flat steel (which is welded to the tubing frame) with -inch by 1 ½-inch bolts.
The electric wires were run from the motor and attached with alligator clips to the vehicle’s 12-volt battery. The meter flow cable lever, with the on/off switch for the 12-volt motor, is mounted to the operator’s plastic seat grab-handle with ¼-inch bolts. The wires and cable are protected and encased in 1-inch outside diameter loom-split poly tubing. The spreader is easily transferred to other vehicles. Jamnik had all of the scrap steel in inventory. With the hardware the project cost about $40. The design, build, electrical wiring and installation took about six hours. GCI
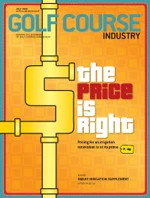
Explore the July 2009 Issue
Check out more from this issue and find your next story to read.
Latest from Golf Course Industry
- Editor’s notebook: Green Start Academy 2024
- USGA focuses on inclusion, sustainability in 2024
- Greens with Envy 65: Carolina on our mind
- Five Iron Golf expands into Minnesota
- Global sports group 54 invests in Turfgrass
- Hawaii's Mauna Kea Golf Course announces reopening
- Georgia GCSA honors superintendent of the year
- Reel Turf Techs: Alex Tessman