
“It's operational, it’s functional and it’s so solid. It’s clean and it’s safe and that’s what matters,” says Matt Delly, superintendent at Monroe Golf Club in Pittsford, New York. Monroe invested in a brilliant new maintenance area and the process was educational.
For Josh Pope, superintendent at The Olde Farm in Bristol, Virginia, the design-and-build process also took several years. Both clubs now have thoughtfully planned facilities that better serve the crew and their operations.

Walls, floors and open doors
At The Olde Farm, there are two sayings on the facility walls. “I wanted to take care of the quotes as soon as we moved in to set the expectation and the culture,” Pope says. On a wall in the break room is the statement “Better Than Yesterday,” which Pope borrowed from Ten Thousand, a fitness apparel company.
Pope and the crew try to be a little better every day. You never know who is going to be on property. The team’s work shines across the championship course and the Orchard course, a 9-hole, par-3, cross-country romp. Both courses were designed by Bobby Weed and the property also boasts a one-acre farm; charming rows of blackberries; and apple, pear and peach trees.
Other common wall decorations are flags from significant tournaments and photos of the crew, the course, or both. Enlarged versions of drainage, irrigation and topography maps are helpful. Place them where people can reference them easily.
Floors should be clean and clutter-free. Wash them regularly and keep pathways open. Doors need to be open too, encouraging communication. The area by the time clock is great for fun announcements or holiday decorations. A little red paint can go a long way to indicate when electrical switches are on or off, particularly for switches being flipped at the start or end of the day. Trash and recycling bins should be emptied regularly.

Renovating or constructing?
Evaluate what can be done internally to move things around by studying the workflow and where inefficiencies exist. Is the break room doubling as a meeting room or do offices serve that function? Who needs an office and how many hours per week is it really used? Can equipment be arranged differently? Over time, things are placed in certain places out of habit. Conscientiously review where everything is and why. Sometimes the most practical answer is a renovation or a wholesale change.
“In the last 10 years, the need for an upgrade in terms of footprint, safety, size, space, all the things that matter became more and more apparent,” Delly says. “We were overdue.”
With Monroe since 2006 and seeing the new facility open in 2020, he has witnessed the full transformation. The building project had a $1.4-million cap and the construction manager was a member who was extremely dedicated to the job, completing the project in about nine months.
“In 2013, we discussed priorities and the five- to-seven-year outlook,” Delly says. “The greens chairman was instrumental in saying ‘How long can we kick this can down the road? We get what we need but you would be surprised if you saw the conditions of the existing facility.’”
He laid out the site and floor plans and described wants and needs. There are seven full-time staff and mid-season the ranks swell to 30 to maintain an 18-hole regulation course, a four-hole short course, the driving range, and chipping and practice greens.
Not all plans made it. For instance, the community zoning regulations didn’t allow onsite housing. The project did meet budget, even with increases in supply costs. “The most important part of this process wasn’t erecting a new building but educating our membership about the conditions of the maintenance facility,” Delly says.
He guided three open tours for more than 200 members and comments such as “this is embarrassing,” “we had no idea” and multiple expletives resounded. He showed everyone the 3D renderings. When it came time to support the project financially, endearingly, 80 percent of members paid the assessment upfront to provide instant working capital.
The site work for the new maintenance area was substantial. More than 100 pine trees were cleared to expand the footprint and comfortably be able to accommodate 18-wheelers. Course maintenance continued with trailers and storage units equipped with lights, heat and A/C. The equipment tech was set up in the old cold storage area.
The new building is 12,500 square feet with an additional 5,000 square feet of cold storage. “My favorite feature is the increased footprint of the entire space, beyond the building,” Delly says. “Cables and wires that were in the way of deliveries are underground now, employee parking flows easily and our bulk storage is huge. We increased space in the locker room, upgraded and doubled the space and fixtures in the restrooms and added a mud room. The equipment technician space and parts room almost tripled and we doubled the space of our sharpening and grinding room. Our chemical storage is away from employee areas. That’s huge.
“We have challenges retaining employees and there were other clubs in the area making facility upgrades too — Oak Hill, Irondequoit and the Country Club of Rochester,” Delly adds. “I will give up experience 100 percent of the time to hire someone who cares and is accountable,” and to compete for those people, the facility has to offer comparable amenities. Employee morale and retention is up, and Delly is pleased. Most facilities will juggle wants and needs with financial resources, but it’s always worth dreaming big and working to see what can happen.
Foreseeing the future
Imagining a facility from the ground up yields more questions. Where is the most functional location for the facility? How big can it be? What’s better: multiple buildings or everything under one roof? What is the optimal timeline?
“At The Olde Farm, I noticed facility needs during my first season,” Pope says. “The facility was in a high-traffic area and the club’s infrastructure and staff has grown in its 20 years. We were in the middle of it all. Where every delivery came. Where cart staging was. There were so many people and so much activity around the building that it wasn’t efficient. We were outgrowing our space for equipment and had a lot sitting outside.”
The general manager and other administrative personnel needed space, so Pope proposed that a new facility be built and the old one repurposed for offices. Plans were debated for a year before committing to separating the maintenance facility from other activity. The first building was 8,000 square feet. The new one is 22,000 square feet.
“The vision set forth by our owner has just grown bigger than ever imagined,” Pope says. “We’re a very private, national golf club. We don’t have that much play but the experience we provide requires the right staff. We had to make sure that we were preparing for the future.” Construction costs jumped between the estimate and breaking ground and a few concessions had to be made but nothing that negatively impacted the operation.
The cost benefits of a new facility can’t be overstated. If workflow efficiency and labor retention improve, that saves time and money. If equipment is better protected and more easily serviced, that is effective asset management. “It’s different with projects on course,” Pope says. “There’s instant gratification and members understand how it pays off because everyone is talking about it. No one wants to come and see the maintenance facility.” Any benefits need to be broadly communicated, multiple times.
Security systems can be an improvement. The new building has a keyless entry. Pope can access different areas with a ring he wears, a swipe card or a fob. It’s quick and he doesn’t need an extra key. The building is set to lock and unlock at certain times. If necessary, the IT department can reference the logs of who is on site. Staff clock in by swiping their fob.
The new facility has alleviated traffic jams. Staff morale is up, mostly due to increased space and better personal facilities. The break room is ample and has multiple refrigerators and microwaves. “I asked staff what they wanted and kept people in the loop,” Pope says. “We viewed renderings and built the excitement.”

The Olde Farm has two houses on the property for interns and they had eight this summer, six for the course and two horticulturalists to help with the farm. The maintenance facility houses three offices, the break room and two locker rooms (men’s and women’s). At a “T” off that is equipment storage and the mechanic’s shop. There is a separate building for chemicals and sprayers.
The project concluded at the start of the 2022 golf season. Pope and the crew went with their instincts about finalizing where everything was going to fit. They will re-evaluate this winter, as time allows. “For those out there trying to get a new maintenance facility who hear ‘no,’ find a different angle,” Pope says. “We know how beneficial they are. Figure out what is best for your property and go back at it.”
At The Olde Farm, they continue to be “Better Than Yesterday.” The second quote, found in one of the main hallways of the maintenance facility is, “In the end, I see the greater purpose of the game to be quite simply the notion of giving back,” stated by Jim McGlothlin, the club’s owner and founder. Pope wants to remind the crew how McGlothlin is inspired. The new facility and their work are because of his vision.
Golf cannot be played without a course. The course cannot be properly maintained without the equipment and the crew. Take care of the people who take care of the equipment and the course. If the maintenance facility needs an upgrade or redesign, motivate the stakeholders who care enough to make those changes.
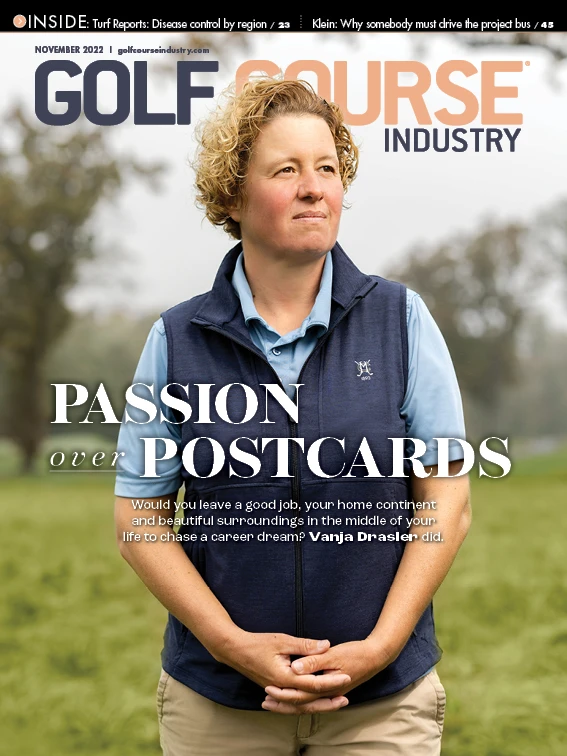
Explore the November 2022 Issue
Check out more from this issue and find your next story to read.
Latest from Golf Course Industry
- Beyond the Page 65: New faces on the back page
- From the publisher’s pen: New? No way!
- Indiana course upgrades range with synthetic ‘bunkers’
- Monterey Peninsula CC Shore Course renovation almost finished
- KemperSports and Touchstone Golf announce partnership
- PBI-Gordon Company hires marketing manager Jared Hoyle
- Mountain Sky Guest Ranch announces bunker enhancement project
- GCSAA names Joshua Tapp director of environmental programs