
Let’s take a walk with a superintendent turned executive of an exclusive private club in a market filled with elite facilities.
Our group consisting of Ohio Turfgrass Foundation members meets Double Eagle COO Todd Voss at the old maintenance building. Before businessman John McConnell decided to build his dream golf course, the light blue structure housed horses. Double Eagle owns a Galena, Ohio, address. Galena was farmland when the course opened in 1992. Today it’s considered part of the bustling and expanding Columbus metropolitan area.
Double Eagle’s prominence also has expanded in the last two-and-a-half decades. Those who rank golf courses often place it in their Top 100 lists. Voss arrived at Double Eagle in March 1991 as an assistant superintendent. Twenty-one years later, he ascended to COO. He remains heavily involved in golf course maintenance, and he spends mornings walk mowing greens.
The club moved its primary maintenance operations to a pair of gutterless red structure behind the 14th green and 15th tee in 2013. The old, blue horse barn still serves a key purpose. It’s where Double Eagle stores chemicals, fertilizer and large equipment. Later, in a quiet moment away from the group, Voss is asked why the club kept the structure. Finding a more open and accessible person in the business than Voss might be tougher than landing a tee time at Double Eagle. Voss visited a dozen maintenance buildings when planning the project.
“Most great clubs have about 20,000 square foot of maintenance, whether that’s cold storage, whether that’s work space, but it’s about 20,000 square feet,” he says. “With our maintenance buildings, we were adding about 7,000 square feet per building. That still makes us a little bit short. By keeping the old building, it allows us a place to put some of the big equipment that just takes up space – tractors, sprayers, backhoes. It also allowed us to now have our fertilizer in a room that has a concrete floor, so that allows a forklift, which is more efficient.”
Do the math: 7,000 + 7,000 = 14,000. That 6,000-square foot difference meant Double Eagle either needed to build a third new building or keep the old one. Chemical and fertilizer storage also factored into the decision. Storing chemicals in the old building prevents Double Eagle from changing current codes and protects the club against potential fire damage, Voss says.
The tour then takes a few detours before visiting the new structures, first stopping at an expansive bentgrass nursery adjacent to the blue building. Native areas, a small pond and trees surround the nursery. The group passes a birdbox – one of 170 – on the walk to the nursery. Multiple emerging bentgrass varieties are tested here. Researchers, especially those from nearby Ohio State, know this part of the property well.
A left turn around more native areas brings the group to the par-4, 14th hole, where first-time visitors immediately notice an absence of markers on tee boxes. The group walks the hole, learning Double Eagle’s maintenance philosophies along the way. Poa annua, in Voss’s words, is “public enemy No. 1 at Double Eagle.” Native areas are left untouched. “What grows in our native areas, grows,” Voss says. Fairways are aerified twice per year; bunkers are viewed as hazards; inputs are limited.
After exiting the 14th green, it’s time to explore the primary maintenance compound. The new and existing buildings are painted red. Completing the compound required two years of permitting, and Voss asked thousands of questions during the stretch. Stories of maintenance building fires convinced him to place mowers and other equipment in multiple buildings. “Did I really want to put all eggs in one basket?” he says. Riding mowers, utility vehicles, walking rotary mowers and handheld equipment are stored in one of the new buildings. Walking reel mowers, staff offices, the equipment technician’s workspace, parts and breakroom are in the other building.
Perhaps the most exhausting and rewarding part of the maintenance compound project involved constructing a covered wash pad. The permitting process lasted nine months. Voss remained persistent, because he’s witnessed too much storm-related untidiness and commotion around the shop in his career. “Just being able to have all the guys wash stuff off at once … it’s time motion,” he says. “You can get it done quicker and easier, and it pays for itself.”
The remainder of the tour includes a stop at the pump station – “That’s our heart,” Voss says – the 15th green, a greenside bunker project on the 12th hole and six-acre irrigation lake built in 2007. The two-hour walk ends at the old maintenance building. Voss fields dozens of questions, and he doesn’t dodge any turf topic during the tour. His advice for colleagues planning a new maintenance facility?
“Ask around,” he says. “If you’re not getting the answer you want, you’re not asking the question correctly. When you visit places, ask them, ‘What do you like about your building? What don’t you like about your building?’ I took our drawing to every superintendent’s meeting and had guys look at it. Maybe you think something is a great idea and somebody goes, ‘This is pretty bad. Let me show you why this is bad.’ You then look at some of these amazing buildings that clubs have built.”

Tartan Talks No. 12
We turned to two ASGCA members to explain the three “Rs” of modern golf course architecture.

Restorations, remodels and renovations served as topics as we joined Steve Forrest and Shawn Smith at Hills & Forrest International headquarters in Toledo, Ohio. The pair revealed their definitions of the misunderstood concepts and implemented examples from their work into the discussion. The podcast also offers tips for superintendents seeking to protect the size of their course’s greens.
Enter bit.ly/2sn7iBE into your web browser to hear the first two-guest episode in Tartan Talks history.
Get curated news on YOUR industry.
Enter your email to receive our newsletters.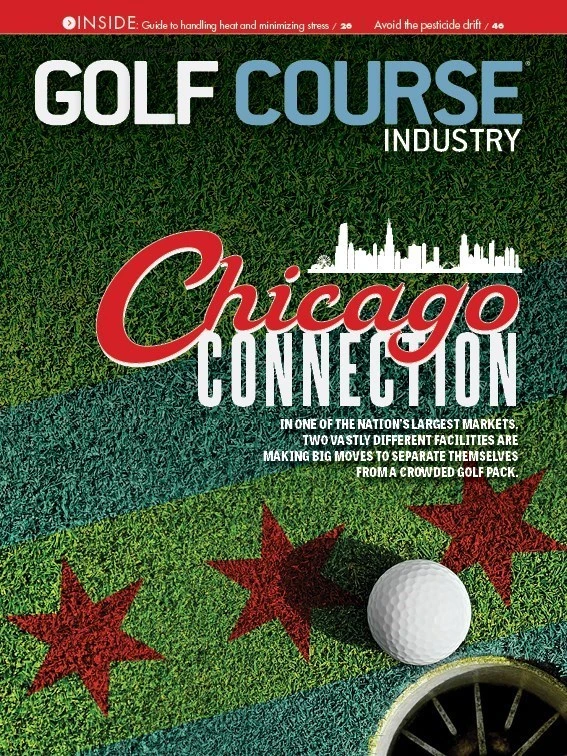
Explore the July 2017 Issue
Check out more from this issue and find your next story to read.
Latest from Golf Course Industry
- Carolinas GCSA raises nearly $300,000 for research
- Advanced Turf Solutions’ Scott Lund expands role
- South Carolina’s Tidewater Golf Club completes renovation project
- SePRO to host webinar on plant growth regulators
- Turfco introduces riding applicator
- From the publisher’s pen: The golf guilt trip
- Bob Farren lands Carolinas GCSA highest honor
- Architect Brian Curley breaks ground on new First Tee venue