In the first two installments of this series about a superintendent’s role in construction (May and July issues), I described contractual boundaries superintendents should work within if acting as an owner’s representative during a construction or renovation project. Below are specifics superintendents should evaluate to ensure a project will be successful.
Turf, fertilizers, amendments
- Verify material for correct quantities and specification compliance, including slow-release components, if any, especially if the contractor is supplying an “or equal” product.
- Monitor the contractor’s initial spreader settings and applications to confirm materials are applied evenly and at correct the rate.
Turf and sod
- Count seed bags and read tags, certification papers, etc., as necessary.
- Measure the cubic feet of each truckload to verify the quantity.
- Visit proposed sod farms to select sod for the project.
- Mark installation limits and direct initial watering.
Greens mix and gravel
- Design or review mix design. Recommend changes within the contract price or through a change order.
- Observe and accept mix and gravel deliveries. Reject those that don’t comply but provide a specific reason for rejection.
- Monitor or provide ongoing mix testing against prototype samples.
Cart path
- Assist with cart-path layout, bridge requirements (weight, width, etc.) and curb location.
- Monitor concrete deliveries and installation. Concrete mix design is usually done by consultants, but the owner’s representative monitors concrete deliveries, including the monitoring of: (i) base compaction and base material installation; (ii) moisture content of the subsoil; (iii) form work and reinforcement installation; (iv) concrete depth; (v) finishing and curing procedures; and (vi) concrete materials.
For the concrete materials:
- Collect delivery tags.
- Perform and/or monitor “slump tests,” which measure how watery the concrete is. With concrete, 4- to 5-inch slump is typical.
- About 30 days after the installation, evaluate the concrete strength by providing or reviewing core cylinder tests after placement to confirm the concrete has sufficient compressive strength (usually specified at 3,000 to 4,000 psi).
- Check for cracks and the need to replace certain areas.
Drainage
This is as important an element of construction as there is, and one you’ll fight forever about, if not done correctly. So, this merits considerable effort to identify drainage-problem areas for correction by grading or pipe additions – including the cart paths, tees and fringe areas after every rain storm – and monitor pipe installation, including: proper line and grade; minimum grade for self-cleansing velocity; and catch basins, including grading around them to assure water enters.
The heartbeat of the golf course – and an area that’s prone to installation problems – is the irrigation system, which requires much of the superintendent’s attention. During a recent project, irrigation consultant Terry Little of Aqua Engineering in Fort Collins, Colo., provided the superintendent with this checklist of things to do or monitor:
- Participate in staking out the system, approving it as you go; and
- Monitor the installation, observing the proper installation of:
- Piping – (i) thrust blocks; (ii) pipe depths, backfill material and routing within manufacturer’s maximum deflection guidelines and “snaked” to allow for contraction; (iii) pipe ends tapered before assembly of bell connections; (iv) properly used PVC primer and cement and removal of excess material from pipes; (v) mechanical joints properly aligned, tightened and installed within manufacturer’s guidelines; and (vi) trench compaction.
- Wiring – 24- and 120-volt wiring and cables should be located: (i) below the pipe centerlines; (ii) loosely to allow for expansion/contraction; (iii) with expansion coils at directional changes; (iv) in a consistent location for future locating ease; and (v) wire splices should be minimal and logically located.
- Sprinklers – set level and swing-joints should be set at 30 to 45 degree angles, not flat on the bottom of the ditch or vertical, and with proper lay length to achieve the correct angle.
- Pump house – Other than the wet well and pump skid, these are often provided by the owner. So, as the owner’s representative, you might take the lead to provide: (i) power to the pumps, meters and transformers; (ii) design criteria and/or review, including leaving room for future needs; (iii) arranging building inspections; and (iv) verifying wet-well depths.
Also, you might encourage good work habits, such as daily clean up, safety programs, meeting any regulations or permit conditions affecting the project. GCI
Jeffrey D. Brauer is a licensed golf course architect and president of GolfScapes, a golf course design firm in Arlington, Texas. Brauer, a past president of the American Society of Golf Course Architects, can be reached at jeff@jeffreydbrauer.com.
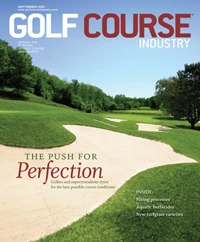
Explore the September 2007 Issue
Check out more from this issue and find your next story to read.
Latest from Golf Course Industry
- Editor’s notebook: Green Start Academy 2024
- USGA focuses on inclusion, sustainability in 2024
- Greens with Envy 65: Carolina on our mind
- Five Iron Golf expands into Minnesota
- Global sports group 54 invests in Turfgrass
- Hawaii's Mauna Kea Golf Course announces reopening
- Georgia GCSA honors superintendent of the year
- Reel Turf Techs: Alex Tessman