WARNING: This is a sea story. It is a work of pure fiction, a hair-raising horror story, purely for your entertainment and education. If you try to check the facts and figures in this sea story, they will be vigorously disputed and denied by all parties involved. People will question my ability, my motives, my integrity, my favorite color, and more ... to discredit this story.
It does not matter who the equipment manufacturer is because all mower companies are moving in the same direction – drive by wire. This is where the operator moves the controls and the signal goes to an array of onboard computers that interpret the operator’s intentions and then, via complex software, cause the mower to act.
Designers love this kind of stuff because, like the Tesla automobile, the physical machine is simpler – just sensors, actuators and computers. The real magic happens in the software. Change the software and you can change the behavior of the machine.
That is how Tesla put 70,000 self-driving cars on the road overnight. For years, they have offered customers a technology package option for $4,000 that was a self-driving car without the software. For the past several years, these cars have been on the road collecting about 750 million miles of driving data and phoning it in. One night in October last year, Tesla downloaded the self-driving software to the cars and next morning 70,000 owners had cars that could drive themselves. You can see why designers would like such things. The same is happening in the turf industry. Every mower company is switching to drive-by-wire. It is cheaper, mechanically simpler, offers more features that you can charge for and is the easiest way for manufacturers to meet air pollution requirements.
THE STORY BEGINS
At engine hour 2979 #4 mower stopped mid stripe on green 13. The driver was unable to get it started using the normal procedure of shutting it off and waiting for the computers to reset and then restarting it 20 times before calling for help. This was early in the morning, so the message was that it would be waiting on the green for me there when I arrived at 7 a.m.
At 7 a.m., I found that the driver had been able to get it running well enough to limp it back to the shop. When I tried it, I could not get it to start and was looking at how to move it inside. The jacking bolts to release the automatic parking brake didn’t work the last time I tried to do that and the steering chain needs to be unhooked before trying to tow it. I was considering bringing in my set of roller skates (car dollies) from my home shop to move when the thing started and ran long enough for me to get it inside the door before it quit running.
The trouble shooting and repair lasted 33 days, involved dealer tech support (now a factory store since they were bought out by the manufacturer), factory tech support, a site visit by a factory tech and discussions with one of the engineers who designed the mower.
The $4,000 I spent on parts, the 264 shop hours I put in trying to get the mower to work, the time the two different tech support departments put in over the phone and the onsite visit by a factory technician did not fix the problem. The mower still had the same constantly changing symptoms it started with.
There was no getting around it. It was time to yell “Uncle!” The only thing left to do was to turn it over to the factory store’s service department and pay the $150 hauling fee, an opened-ended $98/hour, parts extra, for an unknown length of time which when pressed could end up being about $10,000 total.
I was so frustrated that I parked the mower outside to wait for the truck that would pick it up. When the factory store called to say they would be able to pick it up a week earlier than scheduled, I went to move the mower and it started working. I tried mowing a test patch with it and it worked. An experienced driver mowed an entire green with it and got no faults or alarms. The good news is that it has been mowing for a couple of weeks now without one alarm or error message.
What fixed it? My best guess is that baking in the sun for the days that it was outside the shop waiting for the factory store to pick it up cured it. We now make baking #4 in the sun part of each day’s routine.
Get curated news on YOUR industry.
Enter your email to receive our newsletters.
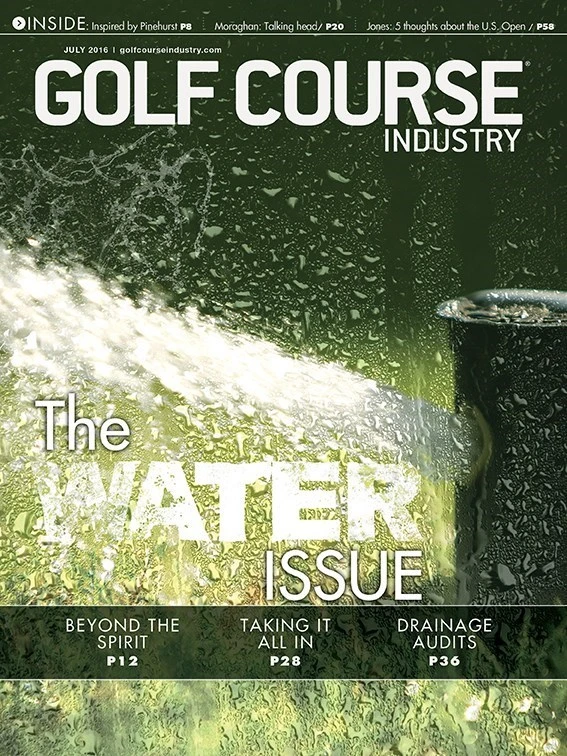
Explore the July 2016 Issue
Check out more from this issue and find your next story to read.
Latest from Golf Course Industry
- Carolinas GCSA raises nearly $300,000 for research
- Advanced Turf Solutions’ Scott Lund expands role
- South Carolina’s Tidewater Golf Club completes renovation project
- SePRO to host webinar on plant growth regulators
- Turfco introduces riding applicator
- From the publisher’s pen: The golf guilt trip
- Bob Farren lands Carolinas GCSA highest honor
- Architect Brian Curley breaks ground on new First Tee venue