How do you make a great course better? Well, at Scioto Country Club in Columbus, Ohio, the grounds crew dug up the greens to find out.
It turns out a renovation at Scioto in the 1960s contaminated the soil profile, preventing the greens from draining efficiently. But because talented superintendents Mark Yoder and Bob Becker babied the greens for years, club members tolerated the poorly draining greens. After a field experiment, Yoder, Becker and architect Mike Hurdzan convinced members their greens needed to be rebuilt.
But the renovation didn’t stop there. The project team moved a few greens, added two sets of tees and regrassed the fairways.
Try this first
In 1974, members of Scioto called Hurdzan to look at winter damage on the greens, and he commented how poorly the greens were built.
“They were very inconsistent,” he says. “It was a first-class golf course, and it needed first-class greens.”
Scioto has had a history of problems with greens – they didn’t drain, says Bob Becker, CGCS.
“The greens were basically big bath tubs,” he says. “We always had complaints about the greens being too soft and overwatered. I chased localized dry spots all day. To work water in, it was delivered by hose. We would use the overhead irrigation only three to four times a year. I was fed up with it.”
From 1980 on, Yoder, now the director of golf course operations, built a USGA-conforming sand layer, but the layer was only 3 inches deep after about 30 years. So Yoder and Becker did what they called the “Scioto Experiment,” in which they double drilled and filled three greens on a few holes using ¾-inch tines.
They then contracted XGD Drainage to install its system on two greens. Their crew cut 19 channels – 14 inches deep and 4 inches wide – into the greens and installed drain tile on 6-foot centers. The process of cutting channels in the greens, including the addition of the Advanced Aer System on only one of the drained greens and the 6-2-2 (sand, soil, peat) profile mix that was added to the trenches, cost $40,000.
There were four greens in the experiment. The first had drainage, an Advanced-Aer unit, and drill and fill. The second had drainage and drill and fill. The third just had drill and fill. The last was a control green. All greens contained RZ wireless sensors at different locations and depths.
“We had so many issues,” Becker says. “We found chunks of concrete, asphalt and steel in the greens. Architect Dick Wilson rebuilt the greens in the 1960s, but we would have been better off with the original Donald Ross greens. The root-zone mix and methods used in the 1960s were horrible. There was no quality control, and the result was inconsistent depths of gravel and root zone. There also was no drain tile under many of the greens.”
The crew used wireless sensors in the greens to measure how much water they were pulling out of the greens. Using information from the sensors, Yoder and Becker were able to plot graphs of the profiles so members could see moisture movement in the greens and the lack of drainage.
“We tried to fix the greens without tearing them up,” says general manager Greg Wolf. “The sensors told us the work we did putting channels into the greens didn’t help at all.”
Selling it to members
Yoder and Becker showed Wolf the results of their experiment.
“It’s always different when it comes from the general manager, not the superintendent,” Becker says. “Members sometimes think the superintendent is just making excuses.”
Yoder and Becker eventually presented the data to the green committee, which made a recommendation to the board of directors. In turn, the membership needed to vote on the suggested greens renovation because the project would change the golf course and the cost required approval from a voting majority. At a town hall meeting about the proposed renovation, members expressed concern about closing their course for a year. That concern was addressed when the club purchased rounds at nearby, recently opened Pinnacle Golf Course. The renovation project was approved by 88 percent of the membership.
“I never thought the members would approve the project to rebuild the greens,” Becker says.
The golf course closed July 9, 2007, and reopened April 29, 2008.
Choosing an architect
The Scioto team chose Hurdzan as the architect for several reasons: He’s local, he’s been a friend of Yoder’s for 30 years and Scioto leadership recognizes the quality of work he does.
“Not everybody will trust you to dust the Mona Lisa,” Hurdzan says.
Several years ago, Hurdzan proposed a golf course improvement plan, including bunkers, that the Scioto membership approved.
“Everyone liked the way the golf course was,” he says. “Membership didn’t want to change what they had because it was good. I thought a few changes could make it better. I won the confidence of the membership. Then I got more aggressive with the renovation.”
Hurdzan says his work on the greens renovation was a continuum of the bunker renovation he did in 2005 and 2006.
“They kept expanding my services in order to satisfy their concerns about the greens,” he says.
New greens
Using LIDAR, Hurdzan mapped out the greens down to one-inch contours, conducted a slope analysis and presented the information to members.
“Some greens were too steep with today’s green speeds, so we softened them a bit,” Wolf says. “With the help of a computer program, we were able to increase the size of the pinnable areas.”
Hurdzan and Norm Hummel from soil testing lab Hummel & Co. were involved with selecting the greens mix from six options.
“The members wanted to make the greens firm and fast, so we added 5 percent soil to the root-zone mix,” Hurdzan says. “It’s a touchy thing to do because the greens can become like concrete. We tested the soil and made sure it remained acceptable.”
The team used an 8-1-1 sand-based root zone that included a soil component at 10 percent to create the desired firmness. The last 10 percent was Profile, which helped keep the performance characteristics of the mix. Before settling on the mix, the team used many variations of each of the mixes on practice greens built on the range in the year leading up to the project.
Wolpert Engineering staked the USGA-spec greens, Becker’s crew stripped them, and Dayton, Ohio-based builder Topp Shape cored them. Then the team restaked the greens and installed the gravel and mix.
“We couldn’t disrupt the outside of the greens – the collars and edges remained the same,” Hurdzan says. “So there was a lot of hand labor.”
In 1989, the greens were regrassed with Pennlinks, and in 1999, they were regrassed again – this time with G2 bentgrass. In 2003, the G2 greens weren’t performing very well, so Becker built a nursery green to test different varieties.
Eventually, Yoder and Becker recommended a combination of A-1, A-4 and T-2 (alpha) on the new greens. The decision was based on a blind test – selecting the plot that survived the practices the best. Becker liked the addition of the T-2 because the A-1 and A-4 are so similar genetically, and he wanted another variety in the mix for diversity. Yoder and Becker educated the project committee about the different varieties, showed them the plots, and the committee approved the superintendents’ recommendations. All the greens were seeded three ways at one pound per 1,000 square feet August 31, 2007.
“We told the members we wouldn’t push the greens,” Becker says. “The height of cut is a little higher. We got to a speed of 9 on opening day and now we’re a 12 on the Stimpmeter at the same height as opening day. We started rolling twice a week, and now we’re up to four days a week. They’re single cut and groomed daily. Next year, we’ll push the greens to what members want.”
Nicklaus’ two cents
On May 28, 2007, six weeks before the start of the renovation project, Jack Nicklaus, an honorary member of Scioto, called the club and said he loved the old course and because he grew up there and felt responsible for bringing in Dick Wilson, he wanted to be involved. Nicklaus came to Scioto and drove around the course with Hurdzan and committee members.
“Jack said, ‘If you want my input, call me,’” Hurdzan says. “Jack called back and was passionate about the job. The committee said, ‘Mike’s our architect.’ Jack said, ‘Fine, we’ll work together.’ Jack came back seven or eight times during the project. I give him credit for making the project better. When Jack says something, people listen more intently.
“I came at this purely from an architectural view,” Hurdzan adds. “Jack looked at it from a player’s view, but we came to the exact same spot. We met dead in the middle. We had a strict budget and weren’t going back to the club for more money.”
Nicklaus moved the greens on holes 8, 10 and 17 closer to water to make shots more challenging. He also moved a few greenside and fairway bunkers.
“He had a lot of fantastic ideas to get the course the way it used to be,” says Tom Topp, v.p. of Topp Shape, who previously worked for Nicklaus at Muirfield Village. “Hurdzan and Nicklaus worked great together. Scioto got the best out of them.”
Widening the scope
What started out with just rebuilding the greens expanded into regrassing the fairways and adding two sets of tees.
“We changed our philosophy,” Becker says. “The members wanted firm and fast and developed a little threshold for browning, so we changed from Poa annua to L-93 bentgass in the fairways. Now we’re using one-quarter of the water, less chemicals and we have better playability.”
Members were able to evaluate L-93 at several courses in the area before choosing to use the variety in the fairways.
“We have an older membership, and they like a little roll, but they didn’t have that with the Poa because we had to water a lot to keep it alive,” Wolf says. “The course is playing more difficult now.”
When it came to the additional tee boxes, the team used the earth removed from the greens to build championship tees, short tees for juniors and higher handicappers, and member tees. There are now six sets of tees.
The crew seeded the fairways during the last 10 days of August 2007 and seeded the tees in September.
“We need 10 to 12 weeks of good grow-in and we got it,” Becker says.
Working together
Members weren’t assessed for the project – the funds came from a capital budget. Scioto purchased everything for the project, and if anything went wrong, Yoder and Becker were responsible. They communicated to members hourly and cleaned up the site every evening.
“Members would come out every night and ask questions,” Becker says. “It’s traumatic to see the golf course they love torn up. They wondered how it would be back the following year. We were visible and answered all questions. It’s a member golf course, and we needed to deliver what they wanted us to do.”
Topp, who had worked for Scioto in the past, was a little stressed about the project but got off to a good start.
“The grounds crew under Becker – their direction and cooperation – had a lot to with the success of the project,” he says. “I can’t say enough about the greens staff. They were always pitching in and helping out. Nobody was trying to take all the credit. The Scioto job was one of the most exciting jobs I’ve had. The project was neat because of the way Mike and Jack worked together and trusted us to put their ideas on the ground.”
Hurdzan praised Topp for doing a herculean job at a high standard.
“He worked long periods of time and did what most thought would be impossible,” he says.
Overall, the project was smooth sailing, Hurdzan says.
“We all had the same focus to produce the best golf course,” he says. “To continue my relationship with Scioto was enormously exciting and rewarding. It’s one of my all-time professional highlights. We took a great golf course and made it better.”
The renovation, though, was about the future, Wolf says.
“This project was about making a championship golf course for the next generation,” he says. GCI
Get curated news on YOUR industry.
Enter your email to receive our newsletters.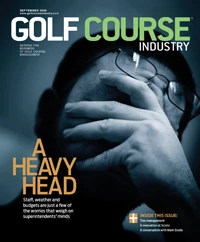
Explore the September 2008 Issue
Check out more from this issue and find your next story to read.
Latest from Golf Course Industry
- Advanced Turf Solutions’ Scott Lund expands role
- South Carolina’s Tidewater Golf Club completes renovation project
- SePRO to host webinar on plant growth regulators
- Turfco introduces riding applicator
- From the publisher’s pen: The golf guilt trip
- Bob Farren lands Carolinas GCSA highest honor
- Architect Brian Curley breaks ground on new First Tee venue
- Turfco unveils new fairway topdresser and material handler