Every year, hundreds of golf courses managers or owners find themselves looking for qualified golf industry equipment technicians, and every year there seems to be fewer available. Many of the equipment technicians in our industry have made the move from the automotive industry or military, while only a select few end up attending college to prepare for the profession. Of those few who attend college, a low percentage seems to stay in the business. Why is that?
For many years, the golf industry looked at technicians as the mechanics, and many course managers and owners throughout the world still have that same view. However, this perception is changing slowly. With the technological advances in equipment and the evolving role of the golf course superintendent, the position is changing rapidly from mechanic to equipment technician – and for some, equipment manager. The old image of a guy holding a wrench just waiting for something to break down is growing into the image of a professional individual who prepares his own budgets and manages a staff, safety programs, facility, etc. The appeal of the position should be changing, yet we haven’t seen an increase of the number of available technicians.
One of the biggest issues is the lack of career awareness. Many people have no idea what a golf course equipment technician is or does. Many people in our industry entered the business by sheer luck or because they knew someone who needed a technician. It’s rare to find someone who knew he wanted to be a golf course equipment technician and took such a direction. We need to encourage qualified individuals to take a serious look at this area of the business.
A second issue is the realization of what the industry is demanding of equipment technicians these days. Many equipment technicians and equipment managers need to have a broad skill set. If you work in the automotive industry, for example, you’re generally working in one specific area, such as oil changes, engines, electronics, transmissions, etc. However, at a golf course, you need to be skilled in all those areas as well as welding, reel set-up, hydraulics diagnosis, electrical systems, computers, etc. Also, think about this: What businesses require someone to be in charge of more than a million dollars worth of assets for an average salary of $35,000 to $40,000 a year? But this isn’t about pay, it’s about making people realize what the industry is asking of technicians. This isn’t something that can be fixed because this is a requirement of the industry. However, identifying demands often can change the sense of urgency.
A third issue most technicians face is poor communication with their supervisor. Take all the aforementioned skills, remove communication, and you have a typical golf course equipment technician’s job. At many facilities, being an equipment technician is a thankless job. One of the rewards is being able to see a beautifully manicured golf course that you helped condition, and for many, that’s all they need. However, when communication doesn’t exist in an operation, you rarely find yourself able to enjoy the results of your work because of time spent scrambling to get things done. This causes frustration and the development of the dreaded “I wish I didn’t have to go in to work today” attitude.
With all this said, how do we address these issues? I’ve always learned that we can’t solve worldly issues until we start at home first. Fixing communication breakdowns, building career awareness and improving attitudes always starts at home. Once technicians see they’re an important part of the team, they become more reliable and are more willing to get things done, and an operation runs much smoother. Superintendents can help technicians by encouraging them to become involved in associations, educational opportunities and equipment decisions. Superintendents should make technicians feel valued. Superintendents will be surprised by how these simple things can elevate an operation from mediocre to excellent.
For those thinking, “I’m not sure about that,” keep this in mind: If you grow the healthiest, most environmentally friendly, greenest turf in the world, how much does that mean if it’s not cut well? That technician is integrally responsible for giving members or guests that impression of “Wow!” or “Man, did you see how bad that looks? I can’t believe we paid to play this course.”
It doesn’t matter if you’re employed by a top 100 course or a 9-hole public facility – they can all be great, but not without everyone working as a team.
It’s the responsibility of every equipment technician and superintendent to ensure that our industry grows and is successful. We need to recruit people to our industry and demonstrate how rewarding it is. However, if we can’t tackle the small issues at home, we can’t expect to grow the industry for the future. GCI
Steven Tucker is the equipment manager at the Ritz-Carlton Members Golf Club in Bradenton, Fla., and the president of the International Golf Course Equipment Managers Assocation. He can be reached at 941-309-2913 or stephen.tucker@ritzcarlton.com.
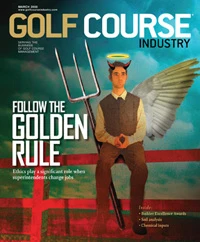
Explore the March 2008 Issue
Check out more from this issue and find your next story to read.
Latest from Golf Course Industry
- The Cabot Collection announces move into course management
- Carolinas GCSA raises nearly $300,000 for research
- Advanced Turf Solutions’ Scott Lund expands role
- South Carolina’s Tidewater Golf Club completes renovation project
- SePRO to host webinar on plant growth regulators
- Turfco introduces riding applicator
- From the publisher’s pen: The golf guilt trip
- Bob Farren lands Carolinas GCSA highest honor