When your members include people known simply by their first names – like Tiger, Shaq and Junior (Ken Griffey); when the foursomes gracing your fairways include Lee Janzen, Mark O’Meara, Darren Clarke, Stuart Appleby, Robert Allenby, Charles Howell III, Craig Parry and Scott Hoch; and when you host what’s expected to become the country’s premier collegiate invitational tournament, you want to stun golfers with the most challenging golf course in the region.
That’s what management at Isleworth Country Club in Windermere, Fla., set out to accomplish when they hired golf course architect Steve Smyers to rebuild completely what they saw as an outdated layout. And that’s what Isleworth and Smyers achieved, even while building multiple tees for middle- and high-handicap players, according to general manager Kurt Kuebler. As proof, Kuebler reported that players from 16 of the top university golf teams in the country, competing in the First Annual Isleworth Collegiate Invitational Golf Tournament Oct. 25 and 26, 2004, scored an average 76 in a practice round on the par-72 course. And they weren’t even playing from the tips.
|
Not lost on the collegiate golfers was that the new Isleworth – transformed for the game of high-tech equipment and long hitters – stretches 7,544 yards and carries a rating of 77.5 and a slope of 142. Previously, the course was 7,179 yards long and carried a rating of 77.5 and a slope of 135.
“We’re now the longest course with the highest slope in Florida,” Kuebler says. “Steve [Smyers] did a terrific job putting together a great multiple set of tees. So if you play the right tee, you’ll truly enjoy this course.”
Smyers says the slope could have been higher but the courses he designs always play harder than the slope because he doesn’t create penalties, he creates obstacles.
“The way [the U.S. Golf Association] calculates slopes is if you go so many feet and don’t have a water hazard, bunker or out-of-bounds marker, it doesn’t consider that a penalty,” he says. “Our obstacles are in a contour, hollow, mound or angle. Conversely, you can always find your golf ball and have the ability to recover on our courses.”
Smyers started from scratch because the old course was torn down.
“This was a massive makeover, not only aesthetically, but from a shot-making perspective,” he says.
While challenging great golfers, Smyers kept in mind the fellow who retires, moves to Florida and wants to play well in the latter years of his life. From the far-forward tees, the course plays 5,747 yards.
“Whenever we build, we design so whoever plays it will become a better player,” Smyers says. “We keep everybody in mind, but we put an emphasis on challenging their shot-making ability and stimulating their thought process.”
A complete change
Isleworth Country Club, which opened in 1986, was designed first by Arnold Palmer and Ed Seay. The 600-acre property, which is almost surrounded by the Butler chain of lakes, serves as Palmer’s answer to Muirfield Village in Ohio, which is replete with flowers and flowering shrubs. Ten years ago, Smyers was hired to renovate all of Isleworth’s 18 greens complexes and surrounds, infusing them with a better setting that still fits the existing layout. He also converted the putting surfaces from bentgrass to Bermudagrass. This time, Smyers worked with then-superintendent David Steel and current superintendent Steve Keller to replace the turfgrasses and irrigation system and craft a course built for 2020.
|
At the same time, Smyers addressed Steel’s and Keller’s maintenance needs – most notably, drainage, irrigation and faster green speeds.
That resulted in changing everything. The course was regraded, creating swells and swales of movement and a range of depth where it was previously flat. Trees were cut down and others planted. Before Steel left the project, Smyers worked closely with him on slopes and contours that might impact mowing.
Smyers didn’t construct his trademark bunkers on every hole, but where he did use them, he did so to catch the eye – to accentuate hilltops and hollows – as a contrast to help golfers read the course and to set up playing strategy.
Slopes also were designed to shed water off the course quickly and efficiently and help with the growth, establishment and daily maintenance of the turfgrasses. To accomplish quicker green speeds, Steel chose TifEagle.
“The scope of work was bigger than a new course,” Smyers says.
Irrigation overhaul
In addition to other work, Lithia, Fla.-based golf course builder Quality Grassing & Services rebuilt 14 greens. The development team worked with the Southwest Florida Water Management District to bring in natural plant material to restore the shorelines and allow the course to feel more in harmony with the lakes. Ten holes interact with water.
Keller, who had recently grown-in 36 holes at Berkeley Hall in Bluffton, S.C., came on board as superintendent during the shaping and irrigation-installation stage. He quickly put his mark on the project, learning the infrastructure, developing a grow-in program, and consulting in the field with Smyers and his design associate Patrick Andrews. He suggested adding drainage basins and adjusting the irrigation system.
“You want to make sure the irrigation heads are located to best fill your needs,” Keller says. “More irrigation is always better, and you need to get it when the getting’s good – that’s during construction. I look at it as if you have only one shot. If you don’t do it right the first time, you’re stuck for years to come.
“Superintendents will be judged on the quality of your turf,” he adds. “As a turf manager, everything is about how water moves and the ability to get rid of it.”
Keller says the most critical irrigation elements for superintendents to understand is the pump station, where the water will be drawn from and making sure it’s installed properly.
“I see a lot of golf courses that put their pump stations in too late,” he says. “They’re concerned about putting in power, and when the pump station comes in, they’re scrambling … in too much of a hurry. I’ve heard horror stories. Our pump station was put in properly. I recommend you get a diver and let him look at where the water is being drawn from, what type of clearance there is, if it’s silty, if you will create a vortex, etc. You should sod the banks of the irrigation lake immediately. When they dig an irrigation lake, over time, the bottom will come up in the process of settling. It’s a problem everywhere.”
Water quality also is crucial.
“You’re only as good as your water, so make sure the area you are drawing from is deep enough and the construction is done properly because silt can be a nightmare.”
Keller says Isleworth has good-quality water because it’s surrounded by deep lakes.
Defining bunkers
Keeping a close eye on the soils, the water table and contours, Keller contributed to the design in ways that will help maintain the course for years to come.
|
To make sure the owner, Tavistock Group, which also owns Lake Nona in Florida, understood the nature of the property well, Smyers wanted to display the ridges, hillsides and cut bunkers into the hillsides to give the course a sand-dune look and feel.
“This is the old dunes of Florida, and we wanted to expose them with high, flashed-up sand,” he says.
To accomplish this, Smyers consulted with Keller to find a product that would prevent bunker erosion. They decided on Bunker-Aid Plus, a fabric to which the sand adheres while allowing water to flow through.
Also, because the bunkers were flashed high, they wanted to ensure the pitch wasn’t too great.
“We hold to the hard, fast, firm concept on the greens approaches, so we worked closely with superintendent and irrigation consultant Mike Pignato on how much water each head controlled, and we made sure we had the right sandy soils to accomplish that,” Smyers says.
Continued work
A treat for Keller was major reconstruction of the maintenance complex. Construction crews gutted and rebuilt everything under the roof, including administrative offices and the locker and break rooms. They also built a recycling and wash-down center, a fueling station and a storage unit for chemicals, fertilizers, divot sand, bunker sand and top soil.
At a glance |
Location: Windermere, Fla. |
Although the golf course construction is complete, the group at Isleworth continues to make improvements. Smyers and Andrews are working with Keller to phase in considerable tree planting.
“Even before the hurricanes, our program included transplanting several hundred trees and thousand flowering shrubs and other plant materials,” Kuebler says. “The storms nearly delayed that process, but we have made a remarkable comeback.”
And the landscaping will continue.
“We will keep working anytime we can enhance the property,” Kuebler says. GCN
Mark Leslie is a freelance writer from Monmouth, Maine. He can be reached at gripfast@ctel.net.
Get curated news on YOUR industry.
Enter your email to receive our newsletters.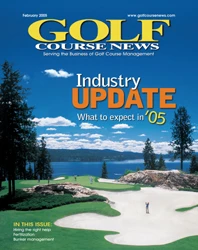
Explore the February 2005 Issue
Check out more from this issue and find your next story to read.
Latest from Golf Course Industry
- GCSAA’s Health in Action 5K/2K reaches fundraising goal
- Landscapes Golf Management to participate in data analyzation initiative
- Reel Turf Techs: Carl Michael
- Atlanta Athletic Club approves funding for master plan
- Maximizing Cultural Practices and Agronomic Benefits with Minimal Surface Disruption
- Real Answers about Spray Nozzle Choices
- From the Course to the Factory: How Customer Insights Drive Innovation
- New & Proven Enzyme Strategies for Sprayable Thatch Management