The challenge for golf facility operators is to deliver a high-quality golf experience continuously and manage costs effectively. Delivering a quality golf experience ensures a golf operation retains its loyal customers and supports maintaining a positive revenue stream.
However, operators don’t always consider golf course conditions as a competitive necessity and don’t plan the facilities that support golf course conditions, specifically the maintenance facility or turf-care center.
Operators can expect to spend $35,000 to $78,000 per hole maintaining a golf course. These figures include payroll, supplies, employee taxes and benefits. Additionally, facilities have made significant investments in maintenance equipment. Many clubs have more than a million dollars worth of equipment and related maintenance items needed for a smooth operation.
Decision making
With all golf facilities, the first priority is the golf course. The second priority are those areas highly noticeable to a club’s membership or the public, such as the clubhouse. The golf maintenance facility is overlooked often. However, it’s imperative leadership reach consensus that something needs to be done.
A method facilities can employ is the use of a strategic/business plan, which would identify issues and clarify goals. A plan establishes a timeline when the issue should be studied and a recommended solution proposed. Then a person or group is assigned ownership of the task. When a business creates a written record, it’s usually followed and most issues can be addressed before they become major problems.
The task of analyzing and studying the maintenance facility normally is assigned to a planning committee, green committee or ad hoc golf planning committee. The task of reviewing the maintenance facility occurs in conjunction with a golf course improvement project. Ideally, this committee is composed of past and present members of the green committee and the board of directors, who represent every segment of a club’s membership. For technical expertise, the committee also might include the golf course superintendent.
The committee also should include the appropriate specialists such as a golf course architect and an environmental specialist. For those committees assigned the task of analyzing the maintenance facility, the participants within this group will change.
The committee’s initial tasks are to study the condition of the existing maintenance facility to determine the scope of work needed in a master plan. From here, an improvement plan for the maintenance facility can be developed with prioritized issues. Then the committee can develop probable cost estimates, which include construction costs and contingency amounts such as cost overruns and an estimate of the financial impact on the golf operation.
The committee also is responsible for communicating with the membership and other parties interested in the project’s development. In a private club environment, space should be dedicated within the club’s newsletter for the chairman of the planning committee or other officer to provide project updates. For municipal and daily-fee operations, the manager/owner is the primary decision-maker regarding the project, consequently consensus is achieved more easily. Within this streamlined environment, it’s helpful to have experienced individuals available to assist with the plan’s development.
A financing plan
With a private club, developing financial options is the most critical success factor in cultivating membership support and approval for capital projects. The most preferred methods of funding a capital improvement are:
Monthly capital dues increase. A club uses a capital dues increase to finance a loan. The advantage of this is that most members prefer a low monthly payment in lieu of a large one-time payment. A member is excused from future payments if he leaves the club. The disadvantage of this financing method is that a loan will put a club in debt, and future member resignations could threaten a club’s finances.
Nonrefundable assessments. The total project cost is divided equally among all golfing members and paid immediately. The advantage of this is that the project is immediately paid for. The disadvantage is it’s the most unpopular method of securing funds with a membership because the high initial cost, and it forces the current membership to pay most of the cost.
Refundable assessment. The upfront assessment can be made more marketable to a membership if the club provides a refundable feature that becomes effective if a member leaves the club. It’s recommended the refundable amount be depreciated during the life of the project. Experience shows the depreciation feature has little impact on gaining member approval for the project, but it will support the club’s future financial profile.
Cash flow from operations. At times, facilities will set aside a portion of their revenue in a capital reserve fund that’s been created for improvement projects. For private clubs, initiation fees or funds generated from a monthly capital fee is normally the source of this revenue. For others, a percentage of green fee revenue might be set aside to fund capital projects. Ideally, operating surpluses would be used to finance golf projects.
The important point is for the owner/operators to monitor their cash flow from operations carefully. The primary revenue source for municipal golf operations is tax revenue. As with private clubs, it’s important for a municipal operation to explain the benefits to the taxpayers of the community clearly.
Facility design and criteria
It might be necessary to use a third party to review the existing facility, provide recommendations and prepare communications for a project related to the maintenance facility. One type of service includes visiting a maintenance facility, reviewing the site and floor plans, conducting a needs analysis, reviewing the maintenance schedule and staffing levels, then comparing the facility to the strategic goals of the course. Along with this analysis, a report can be generated to include an architectural solution and an opinion of probable cost, an outline of specifications and how to proceed with improvements. This process will identify the facility’s shortcomings and propose a solution.
Another type of service is less expensive but still requires a site visit. It includes reviewing the golf course, staffing, maintenance facility site and building floor plans; conducting a needs analysis; and providing a recommendation based on a review of the site and floor plans of the maintenance facility.
Maintenance facility design should attempt to accomplish three objectives. One, provide a safe environment for the employees of the club and golf course. Two, allow for optimal efficiency by the maintenance staff. Three, reduce the risks to the immediate environment. Improper handling and disposal methods at a maintenance facility can create serious environmental problems and potentially expose members and owners to legal liabilities.
It’s essential the facility is well conceived and organized, otherwise a club could be living with a maintenance facility that’s wasteful, fails to address the needs of the operation and exposes the club to legal liabilities, which could include penalties and fines.
Determining the site
Consider a few planning issues when selecting a site for the maintenance facility. For new and existing courses, site identification is important to the design and efficiency of the facility. While some courses will attempt to centrally locate a maintenance facility within the course (see photo at right), other clubs don’t have this option. Consequently, the location of the maintenance facility is on the border of a club’s property, sometimes next to a residential area. Regardless of the location, the site should have enough space to allow for ample traffic circulation. When deciding on a location, several key questions should be answered:
- Does the site provide enough space for buildings the size you want?
- Are there utilities nearby?
- Is there space on the site for fuel storage and dispensing?
- Are natural water sources nearby?
- Is there sufficient space for chemical and fertilizer storage and equipment wash areas?
- Is there sufficient space to allow for the primary structure, ancillary buildings, the delivery of supplies, storage bins and waste-gathering areas?
- Is there enough space to provide employee parking?
- Is there enough space for a loading dock and forklift?
- What are the anticipated reactions from neighbors?
It’s equally important to know if the site being considered is on a floodplain and is suitable for construction. At times, this critical piece of information is overlooked and causes problems when it’s time to secure building permits.
Also, determine if the area is concealed from the golf course. This is usually a consideration when the quality aspects of the operation are reviewed. Whether or not the initial site analysis is favorable, it’s advisable to have a secondary location in mind in case an unforeseen circumstance eliminates the first choice.
For maintenance facilities that care for more than 18 holes, the floor space for each key area should increase 50 percent with the exception of the administrative office spaces.
Building, site requirements
A few planning guidelines should be considered when designing and building a maintenance facility. A total of 10,000 to 13,000 square feet should be allocated for the main structure. Administrative space, primary equipment storage, the mechanics area and possibly an irrigation storage room would be included within the primary structure. The chemical and fertilizer storage building should be separate from the main building. Construction materials should be chosen based on local and federal codes. When reviewing the operation of the site, it’s critical all government requirements are verified to ensure code compliance.
Other planning characteristics:
- The outside area should be paved to support the delivery of equipment and supplies by large trucks. A paved area allows for easy pickup of waste.
- Fuel storage areas should be above ground.
- Outdoor covered storage bins should be used for sand and soil.
- A greenhouse should be included if it’s feasible.
- Waste and Dumpster areas should be included. Consider excavating and paving a bay that puts the top of the Dumpster at ground level.
Primary maintenance facility
The primary maintenance facility structure should include the following:
Administrative space. This area handles the communication of the daily work priorities. The location should be as far away from the equipment storage area as possible. Maintenance logs, invoices and other records must be maintained daily, and a quiet workspace ensures accuracy. Storage should be provided for the maintenance department’s records and supplies. A fireproof cabinet should be used to store material safety data sheets, spray application records, backup irrigation programs and inventory documents – all of which should be duplicated and stored off site.
Climate control is a requirement of this area as well. Computers are used for record-keeping, updating the superintendent’s maintenance procedures and running an irrigation system. Climate control will help computers operate efficiently. If the club’s maintenance and invoice records are stored on a computer in this area, the superintendent should consider having this information backed up daily. A third-party provider might be considered as a resource to back up important records.
Other key characteristics include:
- 1,500 to 2,500 square feet allocated to administrative/break room areas, record storage, etc.;
- Private office space for the superintendent, assistant superintendent, horticulturist, irrigation technician and mechanic and a conference room area;
- A break room or conference room;
- Men’s and women’s locker rooms;
- A guest restroom for club members or visitors; and
- A drying/mudroom to hang and store damp clothes.
The goal of the administrative area is to provide an efficient workspace that promotes communication of daily requirements.
Equipment storage. For most, 6,000 to 8,500 square feet should be allocated to maintenance equipment storage. Floors should be marked so each piece of equipment has a designated space. There should be a small, secure equipment storage area for handheld equipment such as trimmers, chain saws, etc. And there should be optimum circulation so equipment can be driven through, eliminating the need to back up into a space.
Mechanics repair area/parts storage. Most equipment repair areas are 1,500 to 2,000 square feet and are connected to the equipment storage area and the parts storage room. Space should be designated for equipment that’s scheduled for repair. This area should be equipped with a hydraulic lift that positions the equipment for quick repairs and adjustments.
Parts storage in most golf maintenance facilities average 200 to 250 square feet and should be used to store the most frequently used repair items. Some clubs will secure this area with a locked door so the mechanic and superintendent are the only personnel that have access to it. Regardless of access, there should be a direct entry into the equipment repair area so the technicians working on the equipment don’t have to waste time retrieving parts.
Other considerations include an identified area for equipment in repair, an overhead rail system and forced air – with thermostat control – for heat in Northern climates.
Compressor rooms. A separate compressor building is acceptable for Southern climates, but a compressor should be located inside the primary structure in Northern climates. Compressor noise can be distracting to the players on the course and to the neighborhood. A separate compressor room should be provided within the equipment storage area or main repair shop with ventilation and sound insulation.
Grinding room. The grinding room in the main structure of the maintenance facility should be located adjacent to the mechanic’s repair area. It should range in size from 200 to 300 square feet and should support rotary, reel and bed knife grinding. An adequate ventilation system – one that controls the filings – should be available.
Other considerations. Depending on the size of the maintenance facility’s primary structure, other rooms can be introduced. Many operations have added irrigation storage rooms, oil and lubrication storage rooms and equipment tool set-up rooms.
Chemical and fertilizer storage
Chemical storage. One of the most important features of a maintenance facility is the chemical storage building. A maintenance facility should use a separate structure that meets local environmental and safety requirements. The most obvious benefit of a separate facility is safety. If chemicals aren’t stored properly, they could end up in high-traffic areas where the original container could be ruptured.
Another benefit of a chemical storage facility is the ability to contain spills and minimize a club’s exposure to the immediate environment. A dedicated space also promotes an accurate inventory, reducing waste, theft and business order duplication.
Other characteristics include:
- Being located at least 50 feet away from other structures on the site to allow for emergency access and 500 feet away from natural water sources;
- Averaging 400 to 500 square feet – more space is required if a mix/load area is incorporated in the design;
- An all-steel or sealed masonry construction (noncombustible materials);
- Shelving that’s chromed, coated or painted metal or plastic;
- All light switches on the outside of the building, allowing all systems to be activated before entry.
- An electric garage door opener so the building can be opened with entry.
- A fire/smoke/security alarm with a dedicated line to the fire department or security company; and
- Exhaust fans and an emergency shower/eye wash station.
The use of a prefabricated structure should be given consideration when the installation of a new chemical storage facility is necessary. One of the advantages of a prefabricated structure is the different sizes available for the maintenance facility site. Prefabricated structures can range from 62 cubic feet to 2,300 cubic feet.
Other benefits include having all the necessary building, fire and electrical codes met. These structures also are compliant with environmental legislation.
Fertilizer storage facilities. Fertilizer storage areas are equally important, and many of the principles outlined above apply as well. An important feature of the fertilizer storage area is a racking system that has a high weight capacity (18 tons) and is capable of being loaded with a forklift. Other characteristics include:
- Averaging 1,500 square feet and featuring a high weight racking system that can be loaded using a forklift;
- Seamless flooring made of nonskid metal or concrete that’s treated with chemically resistant paint;
- Exhaust fans and emergency wash areas; and
- Meeting OSHA and federal and local EPA compliance.
Mix/load area, storage combination facility. The principle goal of this area is to provide an environment that promotes efficient mixing of chemicals and water-soluble fertilizers while maximizing safety and minimizing environmental risk. Some maintenance facilities have created a combination facility where chemical and fertilizers are close to the mix/load area. Features include: - Being a minimum 600 square feet and connected to the chemical storage facility;
- All-steel or masonry building made of noncombustible materials
- Three bays, one drive through bay as rinsate/mix load pad, one to store products and one to store spray equipment;
- The door height of the entrance should be large enough where the club’s equipment can be parked for filling;
- Two available water sources – potable water for eyewash and safety shower and nonpotable irrigation water to fill the sprayers;
- Exhaust fans with the volume capacity that can exceed six air changes per hour;
- Electric to code with wires in sealed conduit between inner and outer walls;
- Concrete filled steel pipe to protect corners of the building and entryways; and
- Air gap quick cam hose hook ups.
Equipment cleaning. The Clean Air and Water Act is specific about what can and can’t be passed as effluent from the wash-down from an equipment cleaning area. When a club is renovating or building a new facility, the wash-down area should strive to meet three objectives: (1) it must contain 100 percent of the oils, greases, solvents, fuels and any other contaminants found on the equipment; (2) it must be compliant with state and federal environmental protection agencies; and (3) it must be affordable and within the budget of the capital project. Other characteristics include:
- Creating a blowing station that has the ability to remove materials from the equipment prior to washing;
- A wash pad that’s 750 square feet (30 X 25), allowing two machines to be washed at one time; and
- Water recycling systems that are compliant with state and federal EPA requirements.
Environmental resources
Resources for dealing with environmental issues, including the sale, storage and use of pesticides, include the U.S. EPA Web site (www.epa.gov/pesticides/regulating/storage_resources.htm) and the GCSAA’s Web site (www.gcsaa.org). Interestingly, the federal EPA doesn’t have regulations regarding the sale and use of fertilizers. Those requirements are defined at the state level. With regard to water and rinse containment, federal legislation has yet to be adopted. It’s best to review those requirements at the local level.
Follow guidelines
Many times, a maintenance facility is constrained by the physical size of the building site, where the complex is located or by the funding capacity of the operations. When considering the installation of a new facility or a renovation of an existing facility, it’s important the best general practices are observed:
- Ensure the safety needs of the staff are met.
- The facility is organized to minimize the cost of labor and supplies.
- Chemicals and fertilizers should have a defined storage place that can contain a spill.
- The maintenance facility complements the strategic needs of the golf course.
- Compliant with all federal and state EPA and OSHA guidelines.
- Compliant with all local zoning guidelines.
For the physical facility, it’s best to see if plans address the following areas: - Overall site circulation;
- Staff and fleet parking;
- Outdoor storage bins for topdressing sand, bunker sand, mulch and other materials;
- Green waste disposal and recycling;
- Chemical storage and mixing areas;
- Fertilizer storage;
- Fuel storage;
- Equipment wash and rinse containment;
- Equipment storage and circulation;
- Equipment maintenance, including a lift and parts storage; and
- Administrative offices, staff locker and break room. GCI
Michael Vogt, CGCS, is a golf and turfcare consultant with the McMahon Group based in St. Louis. He can be reached at 800-365-2498 or mvogt@mcmahongroup.com.
Get curated news on YOUR industry.
Enter your email to receive our newsletters.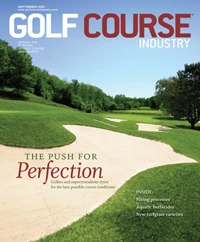
Explore the September 2007 Issue
Check out more from this issue and find your next story to read.
Latest from Golf Course Industry
- LOKSAND opens North American office
- Standard Golf announces new product lineup for 2025
- The Salt Pond taps Troon for management
- KemperSports selected to manage Swansea Country Club
- From the publisher’s pen: Grab that guide
- Introducing our April 2025 issue
- South Carolina leaders honor golf course superintendent
- One and only